FMEAは、故障モードとその影響を分析する解析ツールの1つです。(Failure Mode and Effects Analysisの頭文字)
製造業や医療現場、様々な分野で活用できて、そこにあるリスクを明らかにすることができます。
リスクとは、製造業だと不良品ができること、医療現場だと医療ミスみたいなものです。
不良品を作らなければ会社の利益に繋がりますし、医療ミスが起きなければ大きな信用を得ることができます。
FMEAをうまく活用することで、利益アップ・信用アップ・効率アップなど大きなメリットを獲得できます。
この記事では、FMEAの作り方から完成までの流れをわかりやすく説明します。
- FMEAという言葉を始めて聞いた人
- FMEAをこれから使ってみようとしている人
- 品質管理に携わってる人
動画でみたい人はこちら!
FMEAチームの結成
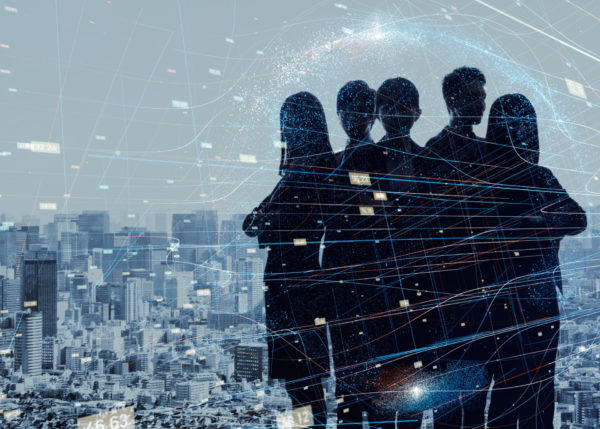
FMEAは1人で作るものではありません。多くの知識・知見を集めることが重要です。
会社の組織をまたいでチームを作ることから始めます。現場に詳しい人、装置に詳しい人、品質管理に詳しい人、技術に長けている人などです。
多くを集める必要はありません。これから作ろうとするFMEAの特定の部分に詳しい人が必要になります。経験則ですが、1つのチームで4~5名がベストだと思います。
1つの製品を作る工程についてのFMEAを作成する場合、幾つかの工程があります。
その場合、工程ごとにその工程に詳しい人でチームを結成します。そしてチームのまとめ役を作りましょう。
リーダーと言っても全体の進行役で問題ないと思います。リーダーが居ないとなかなか進まない事が多いです。
各工程で作ったFMEAをつなげることで、製品の工程FMEAが完成します。
FMEAフォーマットの準備
FMEAも様々な種類があります。いくつか事例を上げると、
- デザインFMEA:ある部品の設計に関するFMEA
- プロセスFMEA:ある部品を作る現場(作業)に関するFMEA
- 装置FMEA:ある部品を作る装置に関するFMEA
などです。FMEAに決まったフォーマットはありません。自分たちが使いやすいフォーマットが最適です。
ただベースとなる考え方はありますので、基本フォーマットを紹介します。
基本フォーマット
左から順番に記入していきます。
- 故障のモードを入れる
- 故障が製品やお客様に与える具体的な影響を入れる
- その故障が与える重要度(影響の大きさ)を10段階で入れる
- 故障が発生する可能性のある原因を入れる
- 故障が発生する発生率を10段階で入れる
- 故障が発生したことが検出できる可能性がある行為を入れる
- 検出できる行為の検出率を10段階で入れる
- 重要度(③)×発生度(⑤)×検出度(⑦)を計算する
⑧で3つを掛け合わせてリスクを数値化します。RPNと呼ばれますが、リスク優先度(Risk Priority Number)の略語になります。
作業ステップの洗い出し
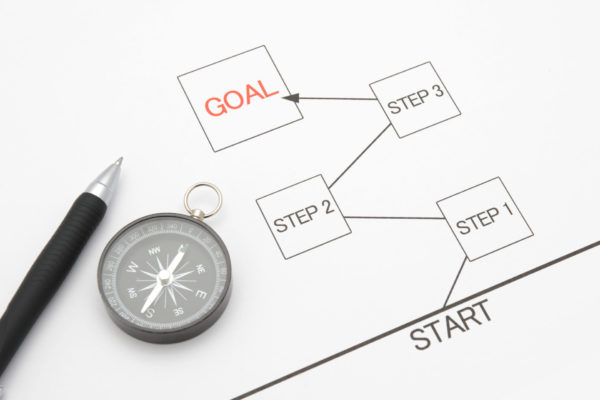
基本フォーマットをベースに、これから作るFMEAを少し使いやすくアレンジすると便利です。ここではプロセスFMEAを事例に紹介します。
その部分を洗い出せるように欄を追加します。
ここでは4つ列を追加しました。
- 工程
- 作業の分類
- 具体的な作業
- 考えられる作業ミス
- 故障モード(基本フォーマットの先頭)
その欄の中に該当するものを記入していきます。
- チーム分けした工程の名称を記入します。
- 工程で行われる作業を大きな括りで分類します。
- 分類した作業の中を1つ1つ具体的な動作で洗い出します。
- 具体的な作業で発生する可能性のあるミスを考えます。
- ミスが起こった場合に発生する故障を入れます。
洗い出しが漏れると、漏れた内容に対してリスクを考えることができなくなります。この洗い出し作業に1番時間をかけましょう。
重要度の点数付け
作業の洗い出しが完了したら、次は重要度を考えます。この部分は基本フォーマットと同じです。
①に故障モードが発生した場合、製品に与える影響を考えます。
材料を間違ったら製品が機能しません。それは不良品になることを意味します。でも、ここで「不良品になる」と記載するのはよくありません。
ここでの影響は、この製品を受け取ったお客様(または後の工程)にどのような影響がでるかになります。
例えば、テレビを買ったお客様に対して「画面が映らない」とか、病院の患者さんに対して、「脈拍が早くなる」などお客様の視点に立った影響になります。
②の重要度は一般的に10段階(1~10)の数値を入れます。
10段階の重要度(影響度)
重要度 | 具体的な影響 |
---|---|
10 | 機能しない |
9 | ある条件下で機能しない |
8 | 機能しない可能性がある |
7 | ある条件下で機能が低下する |
6 | 機能が低下する可能性がある |
5 | 機能するが、改善が必要 |
4 | 機能するが、改善が推奨される |
3 | 影響ないと判断できる |
2 | 無視できる影響 |
1 | 影響なし |
発生度の点数付け
「考えられる作業ミス」に対して、作業ミスがなぜ発生するか、どの程度の頻度で発生するかを考えます。
できるだけ具体的に書きます。
原因が2つや3つになることもあります。その場合は下の行に追加します。
②の発生度は一般的に1~10の10段階で数値を入れます。
10段階の発生度
発生度 | 具体的な頻度 | 頻度の目安 |
---|---|---|
10 | 常に発生する | 毎回 |
9 | 頻繁に発生する | 1回/日 |
8 | 発生頻度が高い | 1回/週 |
7 | よく発生する | 1回/2週 |
6 | たびたび発生する | 1回/1ヶ月 |
5 | 低いとは言えない | 1回/6ヶ月 |
4 | 発生頻度は低い | 1回/1年 |
3 | ごく稀に発生する | 1回/3年 |
2 | ほぼ発生しない | 1回/5年 |
1 | 発生しない | 発生しない |
検出度の点数付け
下表の①には「故障モード」が発生した場合、故障に気付く為に行っていることを書き出します。
②の検出度に下表に応じた数値を入れます。
10段階の検出度
検出度 | 検出レベルの目安 |
---|---|
10 | 検出できない |
9 | 工程での検出率は、10%程度 |
8 | 工程での検出率は、20%程度 |
7 | 工程での検出率は、30%程度 |
6 | 工程での検出率は、50%程度 |
5 | 工程での検出率は、70%程度 |
4 | 後工程で100%検出できる |
3 | 次の工程で100%検出できる |
2 | 作業の中で検出できる |
1 | その場で100%検出できる |
事例で「読み上げて照合」と書きました。一見100%検出することが出来そうですが、人が照合する作業です。
検出レベルの100%は、機械的やソフト・システム的に検出する場合を指しますので、人のミスを考慮して検出率は70%=検出度5を選択しています。
リスク(危険度)の計算
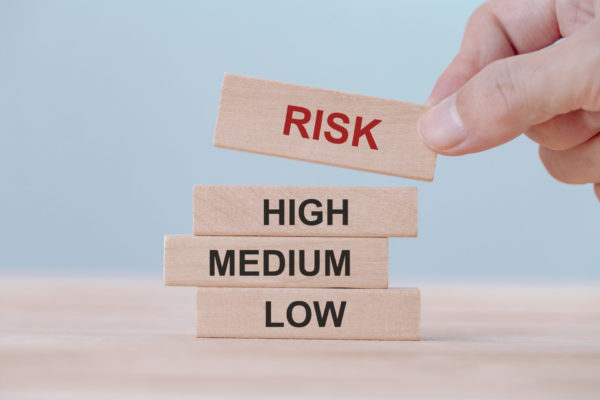
リスクを計算して見ます
リスク(RPN)= 重要度 × 発生度 × 検出度 です。
事例のまとめ
リスクの最大は、1,000ですが、事例では300の結果になりました。
ここまで説明してきた内容で点数付けをした場合、一般的に100を超えると改善する必要があると判断されます。
この材料間違いに関しては、間違いを起こすと重大な不具合が発生する、その発生する頻度も低くないが、それを検出する仕組みが弱いことが分かります。
リスクの考察・対策
FMEAを行った結果、この工程の材料交換で材料を間違う可能性が高いことが分かりました。
では、どうすればいいのか?
材料を間違った場合、重要度は変えることができません。
そのためリスク(RPN)を下げる手段は、発生度を下げる、もしくは検出度を下げるになります。
リスクを下げる方法
この事例で有効な手段は、ラベルを機械的に照合させる方法です。
世の中では当たり前になりつつある方法ですが、材料にバーコードを付け、使うべき材料コードとバーコード照合する方法です。
人のミスを排除できますので、検出度を1にすることができます。
この事例で有効な手段は、材料を1種類にする方法です。間違う可能性がなくなりますので、発生度を1にすることができます。
ただ、経験的に実現することは難しい方法です。また材料の種類ごとにラベルの色を変えるという方法もあります。
実践したことがありますが、発生度を6→5or4にする効果が見込めます。
対策を実施した場合、その内容をリスク(RPN)の後に付け加えて再計算します。
対策を実施することで、リスクを60/50まで下げることが出来ました。
このレベルであれば材料間違いが発生することは無いと判断できます。
まとめ:FMEAは知的財産
FMEAは繰り返し使って蓄積しよう。
- FMEAは正しく使うことができれば、大きな武器となります。
- 作成に時間はかかりますが、1度作ってしまえば、後はそのFMEAを書き足していくだけです。
- 使えば使うほど、経験を重ねるほど強力になっていきます。ぜひ、実践してみて下さい。
- FMEAの精度が上がるほど、知識が蓄積されるほど、工程での不良発生はなくなって、お客様へ流出していく製品もなくなります
FMEAの基本的な考え方や使い方をもう少し理解したい方は「新FMEA技法」が参考になると思います。初心者~中級者向けにかかれた良書です。
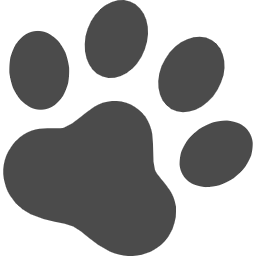
FMEAはコアツールの1つです
FMEA(故障モードとその影響分析)は、自動車の国際品質規格IATF16949のコアツールの1つです。
不良品を発生させない、流出させない考え方は、故障してはいけない自動車部品のモノ作りに必要だからです。
- APQP(先行製品品質計画)
- FMEA(故障モードと影響解析)※この記事
- CP(コントロールプラン)
- MSA(計測システム解析)
- SPC(統計的工程管理)
- PPAP(生産部品承認プロセス)
興味のある方は、それぞれ個別記事にジャンプしますので参考にしてみてください。
IATF16949に欠かせないコアツールの使い方を解説した基礎講座を作成しました。
有料記事(490円)となりますが、IATFのコアツールを体系的に理解することができます。
冒頭部分は無料ですので、応援いただける方は購入してもらえるとありがたいです。
よろしくお願いします。<(_ _)>
本記事は以上となります。最後までお付き合い、ありがとうございました。