自動車関係の仕事をしてる会社だと、国際規格IATF16949の取得が要求されることがあります。
IATF16949の要求事項の中には、製品を作るときに必要なFMEA、コントロールプランがあります。
IATF16949は、海外の自動車メーカーを中心に作られた品質管理の国際規格なので、日本ではまだ浸透していない感がありますが、海外メーカーとの取引には必須な考え方です。
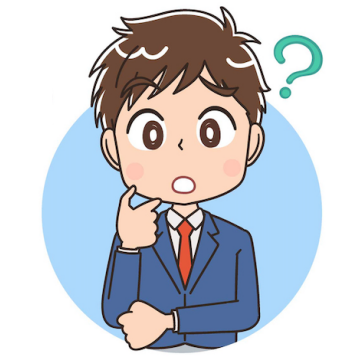
コントロールプランって、なに?
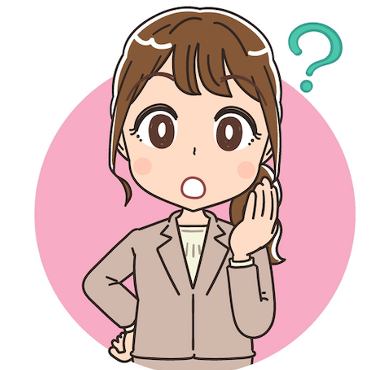
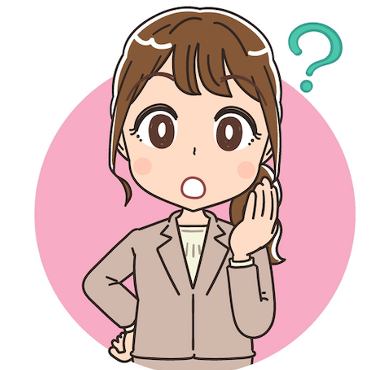
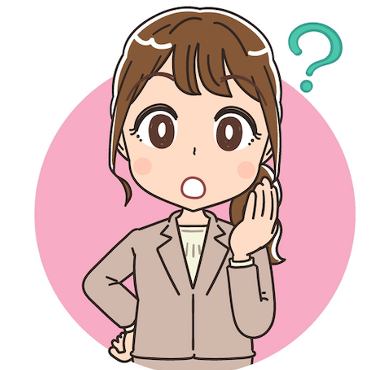
何となく作ってみたけど、これでいいのかなぁ・・



コントロールプランって、どうやって使うんだろう?
この記事では、そんな疑問を持っている人に、コントロールプランの事例を使ってわかりやすく解説します。
- コントロールプランを初めて作る人
- これからIATF16949の審査を受ける人
- これまで何となくコントロールプランを見てた人
動画での解説はこちら
コントロールプランとは?
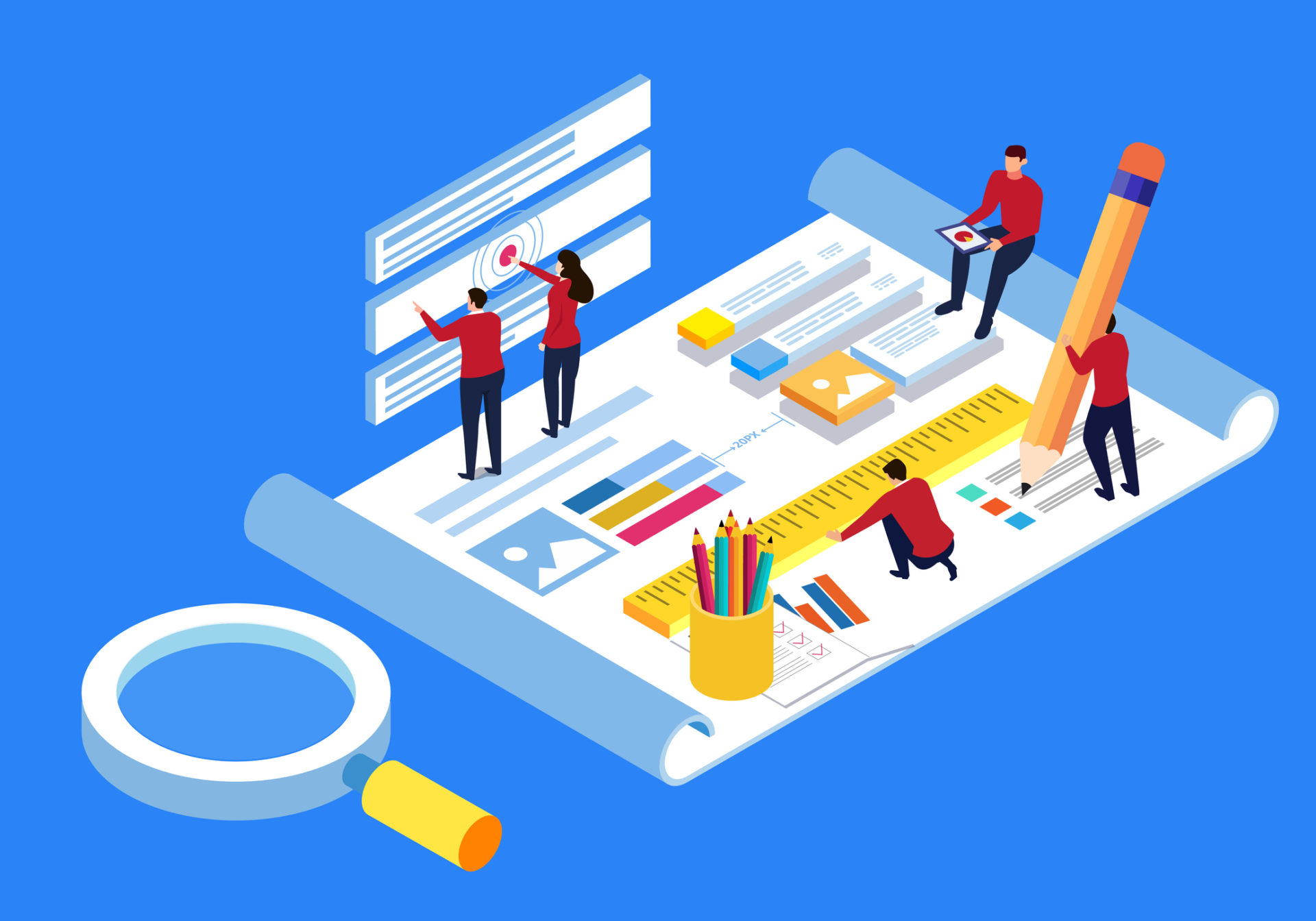
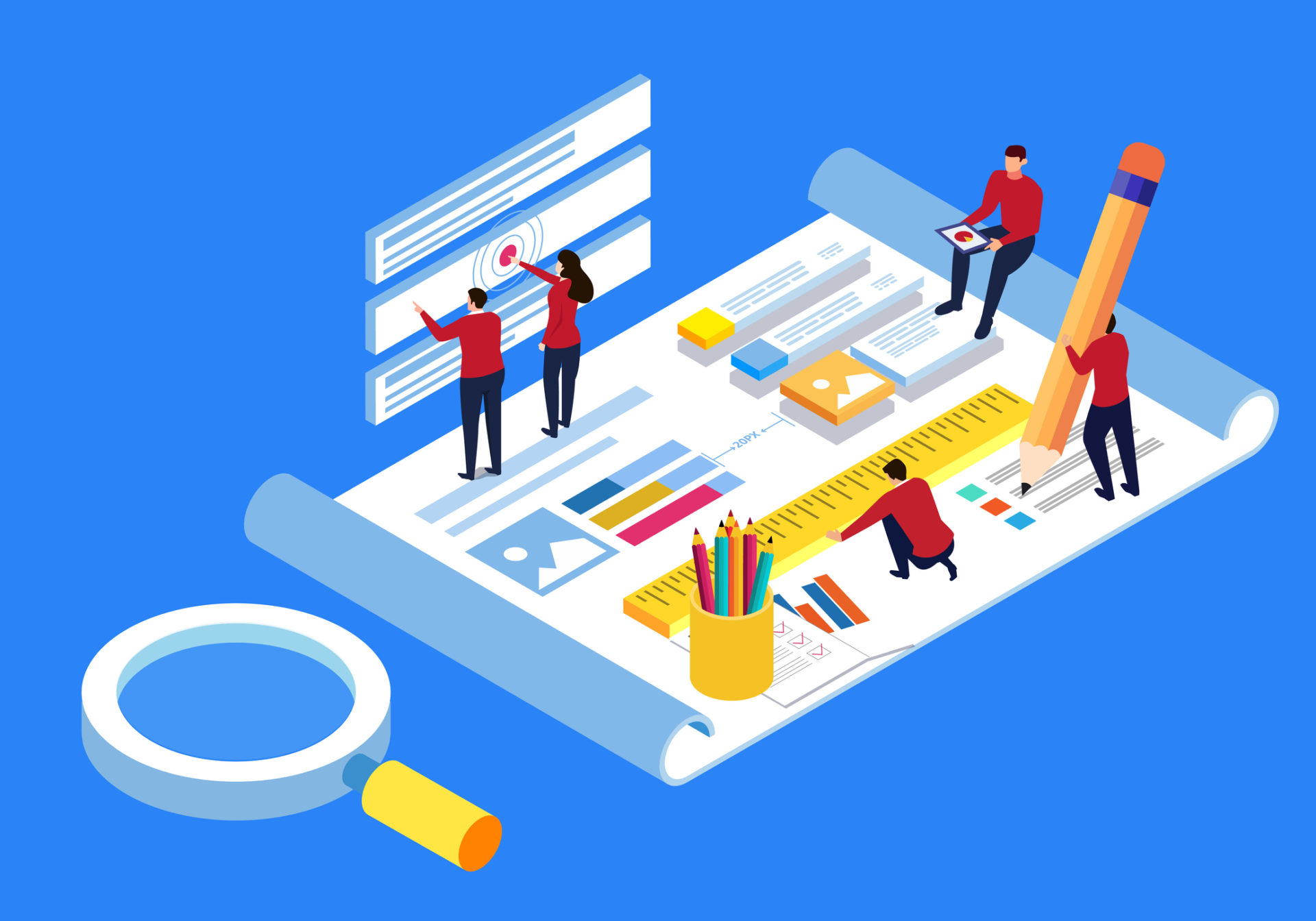
コントロールプランは、製品を作る過程をまとめた工程の設計図です。
大きく試作コントロールプランと量産コントロールプランの2つがあります。
- 試作コントロールプラン
-
製品の開発・設計段階で作られるものです。開発・設計を進めていき、実際の試作製品を評価することで、修正が加えられていきます。
- 量産コントロールプラン
-
試作コントロールプランの最終版が、量産コントロールプランになります。量産コントロールプランに沿って、実際に製品を製造すれば問題なく製品が出来上がります。
工程QC図と似ているので、少し補足です。
もともと日本で作られた工程の設計図です。QC工程表やQCSフローチャートと呼ばれることもありますが、同じものと思って問題ありません。
コントロールプランとの違いは、決まったフォーマットが無いことです。それぞれの会社が使いやすくアレンジして作られてます。
一方、コントロールプランはIATF16949規格の中でフォーマットが決まってます。
IATF16949のフォーマットを使用した工程設計図が、コントロールプラン。IATF16949のフォーマットを使っていない工程設計図が、工程QC図と覚えておけば良いと思います。
コントロールプランの様式
IATF16949で定められているフォーマットを日本語版にしてみました。
このフォーマットを使って「部品を切断する工程」を例にコントロールプランを作ってみます。
切断工程のコントロールプラン
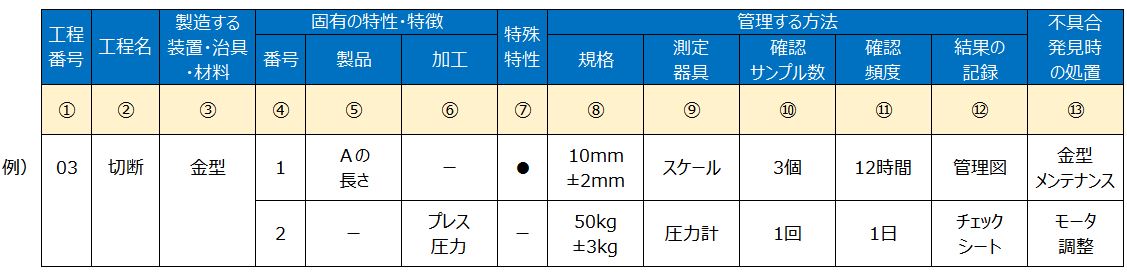
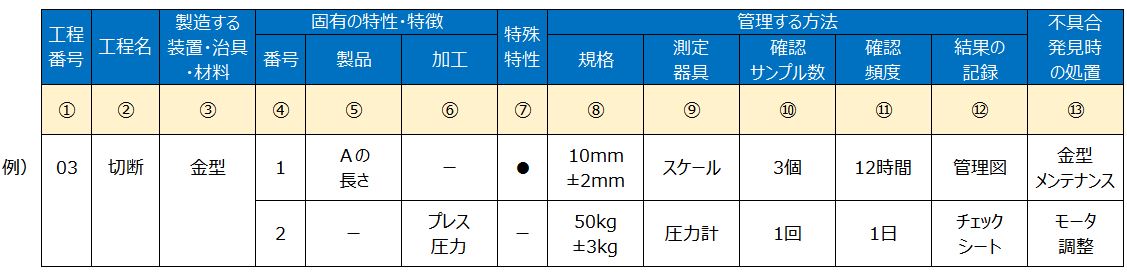
それぞれの項目に番号を付けましたので、各番号について何を意味するか説明します。
- ①工程番号
-
コントロールプランは、部品を作る為に工程を順番に書く必要があります。上から順番に作業することで、1つの部品が完成します。
工程番号は、1番から順番に連番が付与します。
- ②工程名
-
部品を作る上で、区切りとなる工程の名前を記載します。
- ③製造する装置・治具・材料
-
部品を作る上で必要な装置、治工具、材料を1つずつ全て書き出します。
ここに記載されているものを使用する必要があります。間違ったものを使うと不良品を作る原因になります。
- ④番号(固有の特性・特徴)
-
1つの工程で管理する項目について、1から順番に連番を付けます。
- ⑤製品(固有の特性・特徴)
-
金型を管理する上で必要なことを記載します。「製品」と「加工」にわけましたが、「製品」の欄には金型で出来上がったモノに対する管理を書きます。
ここでは、出来上がった製品のA部分の長さを測定して、金型が正常に動作出来ているかを確認する目的です。
- ⑥加工(固有の特性・特徴)
-
この欄には、金型が動作する上で必要な条件や設定といった機械的な管理の内容を記載します。
⑤の製品がアウトプットの管理に対して、⑥加工はインプットの管理です。ここでインプットの内容を明確にします。
- ⑦特殊特性
-
難しい言葉になりますが、製品を作る上で最も重要な管理するべきポイントにマークを付けます。
マークの指定はありませんが、その会社や組織ではマークを指定する必要があります。ここでは「●」で表現しています。
特殊特性に指定された項目は、工程能力Cpkの把握やSPC管理が求められます。
SPCを詳しく知りたい人はこちらの記事で解説してます。
- ⑧規格
-
⑤の製品、⑥の加工を管理する為の上限値、下限値を記載します。
基本的に、狙うべき値を明確にした方が良い為「◯±◯mm」といった表現が好まれます。センター値を狙う必要がない場合は「◯~◯mm」といった記載方法でも大丈夫です。
- ⑨測定器具
-
何を使って長さや圧力を測定するのかを明確にします。ここに記載された測定器具は計測器管理が必要になります。
計測器管理(MSA)とは、その測定器が正確に測定できていることを保証するものです。
MSAが詳しく知りたい人はこちらの記事で解説してます。
- ⑩確認サンプル数
-
1回の測定に必要な製品の数量や回数を明確にします。
- ⑪確認頻度
-
測定する頻度になります。12時間ごとに測定するや1日1回測定することを明確にします。
- ⑫結果の記録
-
測定した結果を何に記録するかを明確にします。例で管理図と書きましたが、Xbar-R管理図やP管理図など、具体的な管理図の名前も記載します。
本来、この部分はControl Method(管理方法)の欄です。測定した結果を記録して、その結果を見て良否を判断するまでが必要になります。
- ⑬不具合発見時の処置
-
もし、測定した結果が規格から外れていた場合に何を行うかを記載します。
実際には、外れた原因を調査して、調査結果からアクションが決まります。この欄には、その手順が書かれた文書の番号や名称が記載されることが多いです。
コントロールプランの使い方
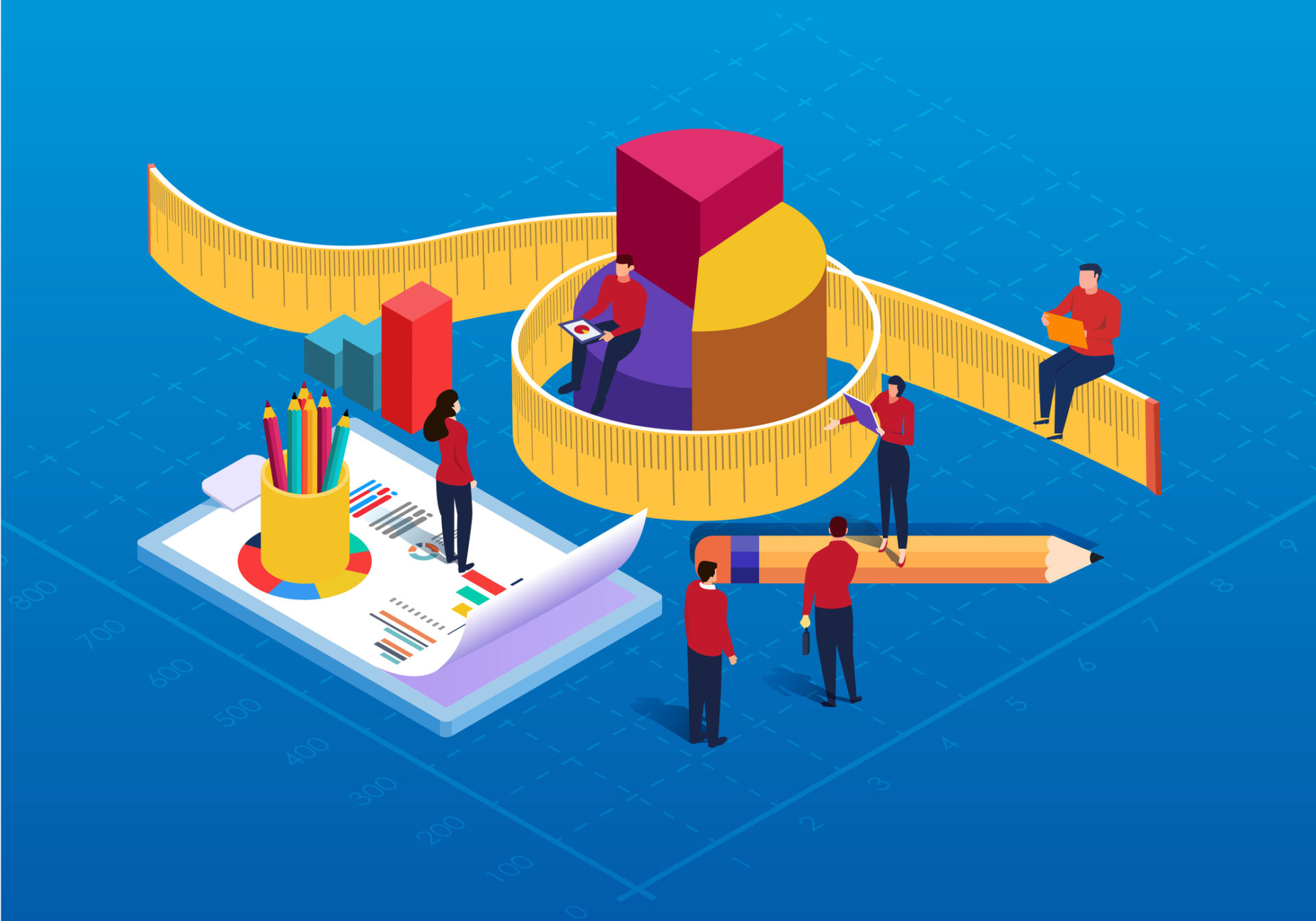
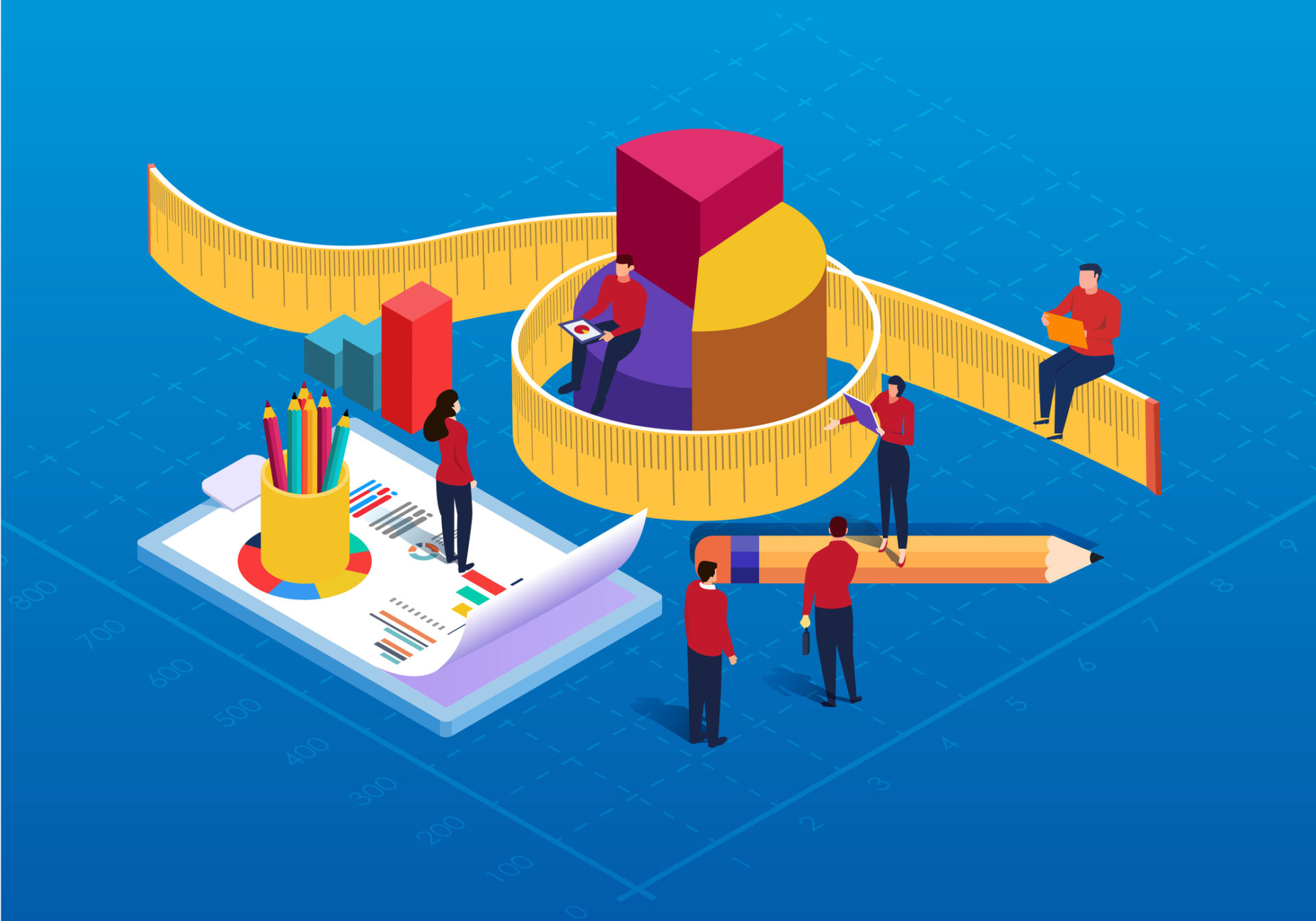
コントロールプランの様式に沿って、工程の入口から出口までを順番に書いて行きます。ここでは、一般的な工程の流れを解説します。
基本的に作られる部品の視点に立って、5M1Eの観点で「製造する装置・治具・材料」の部分を埋めていきます。具体的な5M1Eで考えると
- 環境
-
作業するエリアの温度や湿度、材料を保管する温度や湿度、場合によっては静電気の対策なども含まれます。
- 材料・製品
-
作業に使う材料、これから作る部品や製品を全て書き出します。
- 装置・治工具
-
製造に使う装置や治具、金型や工具などを含めます。
- 作業の方法
-
加工の条件や点検の方法、作業の方法を明確にするものです。事例の表では「加工」の欄に当たります。
- 作業者
-
人の動きが介在する箇所になります。事例の表では「製品」欄の「運搬」などに当たります。
- 検査・測定
-
部品の検査や測定が必要かを書き出します。事例の表では「製品」欄の「検査・外観」に当たります。
5M1Eの具体的な内容を知りたい人は、こちらの記事で解説してます。
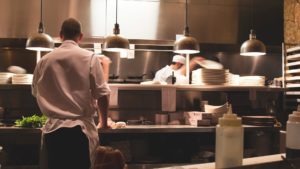
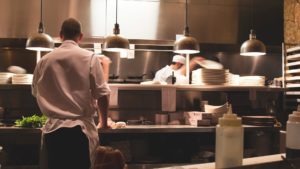
工程で使用しているものを全て書き出して、1つずつ5M1Eの視点で考えていくことで、コントロールプランが出来上がります。
ちょっと面倒ですが、コツコツ実践するのみです^^
これからコントロールプランを作成する人の参考になればと思います。
最後までお付き合い、ありがとうございました。<(_ _)>