みなさん、こんにちは!
製造業の現場で25年ほど品質管理の仕事をしてます。ぱぱくまと申します。
APQPは、IATF16949にかかわる仕事をしてると、たびたび登場するワード。
日本語に訳すると「先行製品品質計画」です。
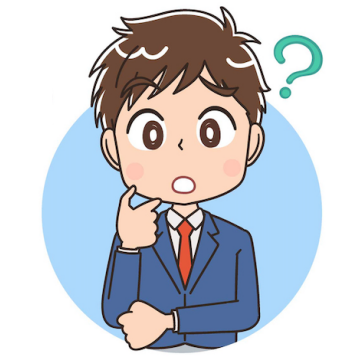
先行製品品質計画!?
聞いたことないんだけど・・
日本語にすると、わかりにくいですよね(^^;
この記事では、APQPが具体的にどんなことを意味するか、初心者の方にわかりやすく解説します。
最後まで読んで頂くと、製品がどうやって設計されて、現場で作られるようになるかがわかります^^
- これからIATF16949の仕事に関わる人
- なんとなくAPQPという言葉を使ってる人
- コアツールの理解を深めたい人
APQPって、なに?
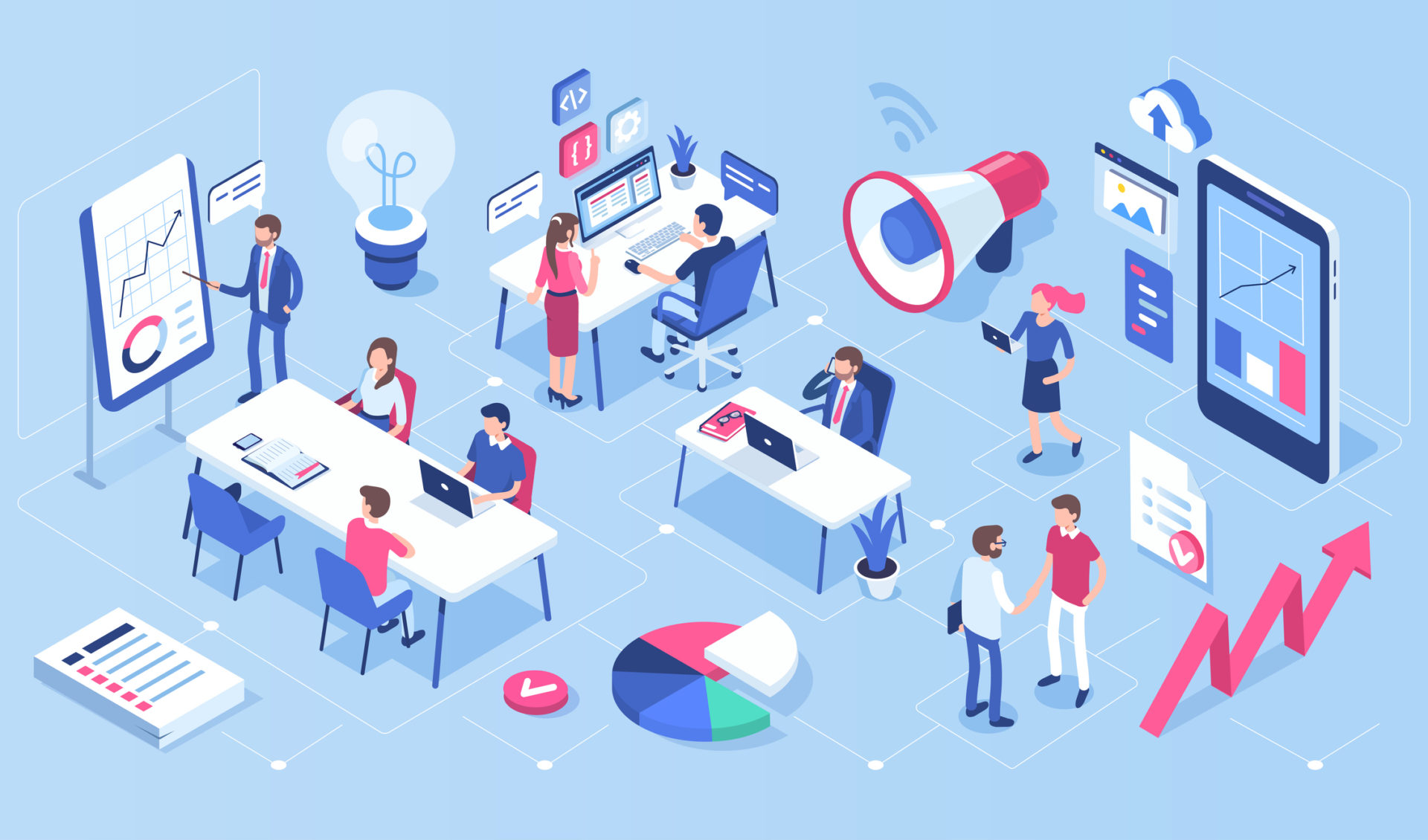
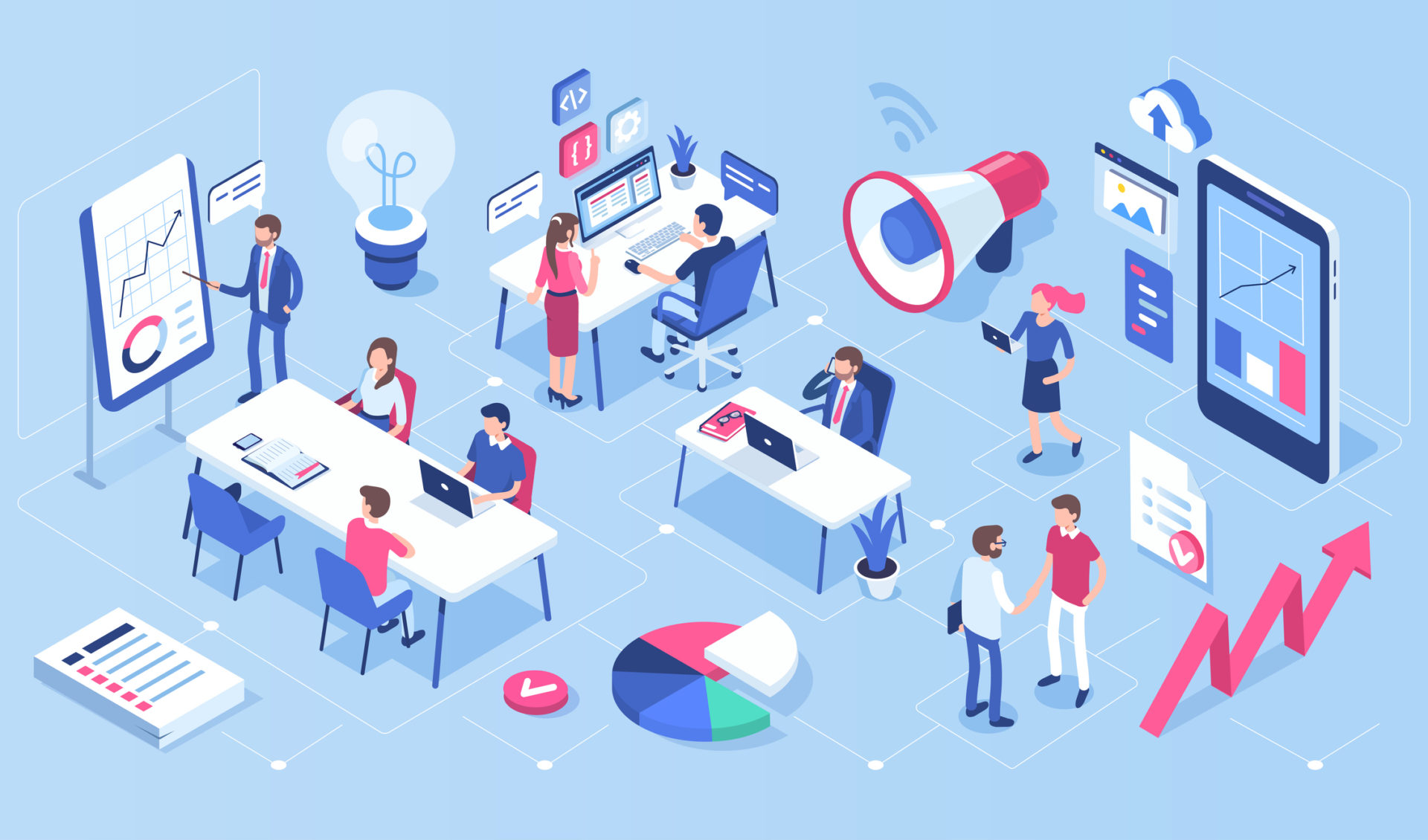
APQPは、ある1つの製品や部品を作るときに立ち上げられるプロジェクトのことです。
これから製品を作ろうとする場合、いろんなことを考えないといけません。
- なんの目的で作るのか?
- どんな製品を作るのか?
- 誰をターゲットに製品を売ろうか?
- どこの工場で作ろうか?
- いつ発売しようか?
- 値段は、いくらにしようか?
そんな問題を解決するチームの活動が、APQPです。
例えば、映画を作るときのプロジェクトチーム「名探偵コナン製作委員会」とかです^^
APQPを進めるためには、大きく6つのステップがあります。
- チームを作る
- 計画を作る
- 設計する
- 設計を具体化する
- 試作して検証する
- 量産する
それぞれ具体的に説明します。
一般的には「チームを作る」と「計画を作る」を一緒にして5段階のフェーズで活動します。
この記事では、わかりやすくするために最初のチーム作りも含んで6段階にしてますので、ご了承ください<(_ _)>
チームを作る
それぞれの専門知識を持ったメンバーを集めます。
- 営業:市場のニーズを調査する人
- 技術:製品の設計をする人
- 品質:製品の品質を保証する人
- 製造:実際に製品を作る人
- 設備:製品を製造する機械に詳しい人
いろんな職種の人が集まるため、「多機能チーム」とか「部門横断的チーム」と呼びます。
ただ、実際の現場ではAPQPという言葉自体がプロジェクトとかプロジェクトチームの意味で使われます。
多機能チームって、なんか馴染みがないですもんね(^^;
プロジェクトリーダー(APQPチームリーダー)には、設計に詳しい技術職の人がなるのが一般的です。
計画を作る
顧客ニーズや市場調査から、売れそうな製品を作る計画を立てます。
- どんな製品を作るか
- いつまでに作るか
プロジェクトチームは、データ(インプット)から計画書類(アウトプット)を作成します。
このときアウトプットする全体の開発スケジュールをもとに、次の設計や試作が進められます。
設計する
「計画」でイメージした製品を形にするために設計図を作ります。
- どんな材料を使うのか
- どんな加工をするのか
- 加工する条件は何にするのか
- どんな箇所に不具合につながる危険性があるのか
ここで作られるFMEA、コントロールプランが実際にものを作る上で重要な役割をはたします。
- FMEAは、不良を作らないために、どうすれば良いのかの指標
- コントロールプランは、モノを作るための設計図
設計を具体化する
設計した図面にもとづいて、実際に製品を作ってみます。最初の試作品です。
この試作品で起こったトラブル、問題箇所をFMEAとコントロールプランにフィードバックして完成度をあげます。
アウトプットの言葉が少し難しいので、補足説明します。
工程FMEA
工程FMEAは、製造ラインで起こるトラブルを予防するための解析方法です。
設計FMEAをベースに作られます。設計FMEAと工程FMEAの違いは、どこに焦点をあてているかです。
設計FMEAは、モノのデザインそのもので発生するトラブルに焦点をあてています。
例えば、大きな車に小さい容量のバッテリーを取り付ける設計をして、電池がすぐなくなるようなトラブルです。
車の大きさとバッテリーの容量に問題がないかをチェックする手法に設計FMEAが使われます。
一方で工程FMEAは、製品を作るときに発生するトラブルに焦点をあててます。
例えば、車のタイヤを取り付けるとき、ネジの締め付けがゆるくてタイヤが取れた!ようなトラブルです。
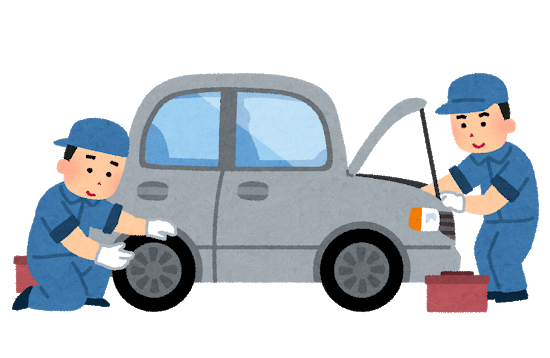
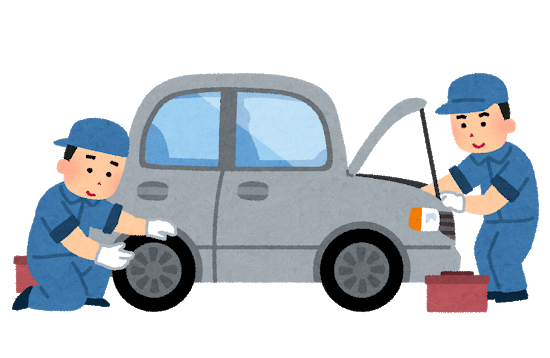
ネジを締め付ける力は問題ないのかをチェックする手法に工程FMEAが使われます。
量産試作コントロールプラン
試作コントロールプランに、現場の管理を加えたコントロールプラン。ほぼ、これをベースに量産が行われます。
量産試作で起こった問題をフィードバックして、最終のコントロールプランが完成します。
フロアレイアウト
フロアレイアウトは、現場の機械や人の動線に問題がないかチェックする目的で作ります。


実際は、すでにあるラインで作業する場合が多いので、モノの流れる動線がおかしくないかをチェックする意味でフロアレイアウトを作ります。
現場のレイアウト図に、作業の順番通りに線を引いていきます。
MSAの計画書
MSAは、計測器管理にでてくる言葉です。
MSA=Measurement(計測) System(システム) Analysis(解析)の頭文字。
少し難しいですが、「現場で使う測定器が正しいか?」をチェックする仕組みだと思えばOKです。
どの計測器を使うかの計画を立てます。
MSAに関する詳しい解説はこちらの記事で解説してます。
SPCの計画書
SPCは、データに基づいた工程管理にでてくる言葉です。
SPC=Statistical(統計)Process(工程)Control(管理)の頭文字。
現場では、製品を作ったあとに正しくできているか測定してデータを取ります。
これまで取得したデータを使って、不良を作る前に、統計的な傾向をつかんで手を打ちます。
ここでは「どの測定項目をSPCにするのか?」の計画を立てます。
SPCに関する詳しい解説はこちらの記事で解説してます。
試作して検証する
試作品を作る回数を増やして、量産できるかを確かめます。「製品と工程の妥当性」という言葉がよく使われます。
量産と同じような数量を作ってみて、製品の不具合やライン作業に問題がないかの最終チェックです。
ここでも少しアウトプットの補足です。
PPAPの提出
PPAPは、直訳すると「生産部品承認プロセス」。製品に関するデータ一式をお客さんへ提出して、認めてもらう手続きのことです。
PPAPは、「Production Part Approval Process」の頭文字を取った略称。
提出する書類は決められていて、全部で18種類もあります。
かなり大変ですが、これを提出してお客さんに承認してもらわないと、製品が納品できません(^^;
PPAPに関する詳しい解説はこちらの記事で解説してます。
量産する
量産がはじまれば、APQPの活動は一旦落ち着きます。
あとは、量産で得られるデータをモニタしつつ、製品の品質が安定するように維持継続、改善活動を行います。
このとき、モニタするデータは、SPCや特殊特性の工程能力数値です。
データに問題がある場合は、なにが原因かを調査して、改善することで、安定した製品を作っていきます。
AQPAは、コアツールの1つ
APQPは、コアツールの1つになっています。
コアツールは、全部で6つ。
- APQP(先行製品品質計画)
- FMEA(故障モードと影響解析)
- CP(コントロールプラン)
- MSA(計測システム解析)
- SPC(統計的工程管理)
- PPAP(生産部品承認プロセス)
コアツールは、全て品質を保証する上で大切な考え方です。
APQPは、そのコアツールのスタートからゴールまでを見守る役割を担ってます。
「APQPにはじまり、APQPに終わる」って感じです^^
コアツールの詳細はこちらの記事で解説してます。
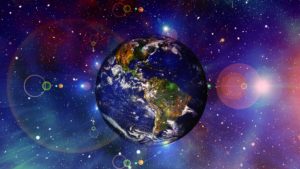
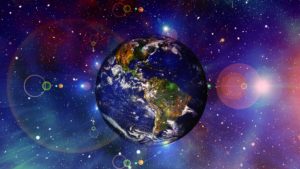
本記事は以上となります。
この記事が「APQP」を調べている人の参考になれば幸いです。
IATF16949に欠かせないコアツールの使い方を解説した基礎講座を作成しました。
有料記事(490円)となりますが、IATFのコアツールを体系的に理解することができます。
冒頭部分は無料ですので、応援いただける方は購入してもらえるとありがたいです。
よろしくお願いします。<(_ _)>
最後までお付き合い、ありがとうございました。m(_ _)m