製品の品質保証だと国際規格のISO9001が一般的、自動車向けの部品だとIATF16949(旧:ISO/TS16949)がメジャーだと思います。
でも最近、日本でもVDA6.3という言葉をよく聞くようになってきました。VDA6.3は、ドイツの自動車メーカーが作った協会が推奨する品質規格の名前。
イメージ的には、下のピラミット図のような位置関係にあります。IATF16949をより具体的に、生産工場の現場に焦点をあてた感じです。
ISO9001やIATF16949は、専門機関が審査をしますが、VDA6.3は直接部品を買うメーカーが監査します。
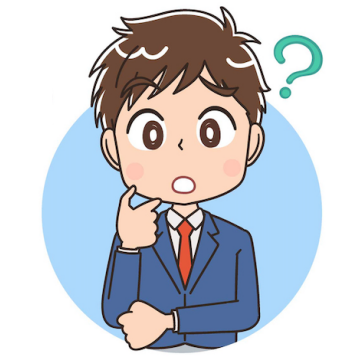
じゃあ、VDA6.3って具体的にどんな審査するの?
VDA6.3の監査は、専用のチェックシートがあって、聞かれる質問の内容も決まってます。
この記事では僕の経験則をまじえて、VDA6.3の監査で質問される内容を噛み砕いて解説します。
これからVDA6.3の監査を受けたことがない人にだいたいのイメージを持って頂ければと思います。全てを網羅してる訳じゃありませんが、知っておいて損はありません。
IATF16949とVDA6.3との違いを知りたい人はこちらで解説してます。
- これからVDA6.3監査を受ける人
- ドイツの自動車メーカーへ部品を納めている会社の人
- 自動車部品の品質管理に携わってる人
VDA6.3って、なに?
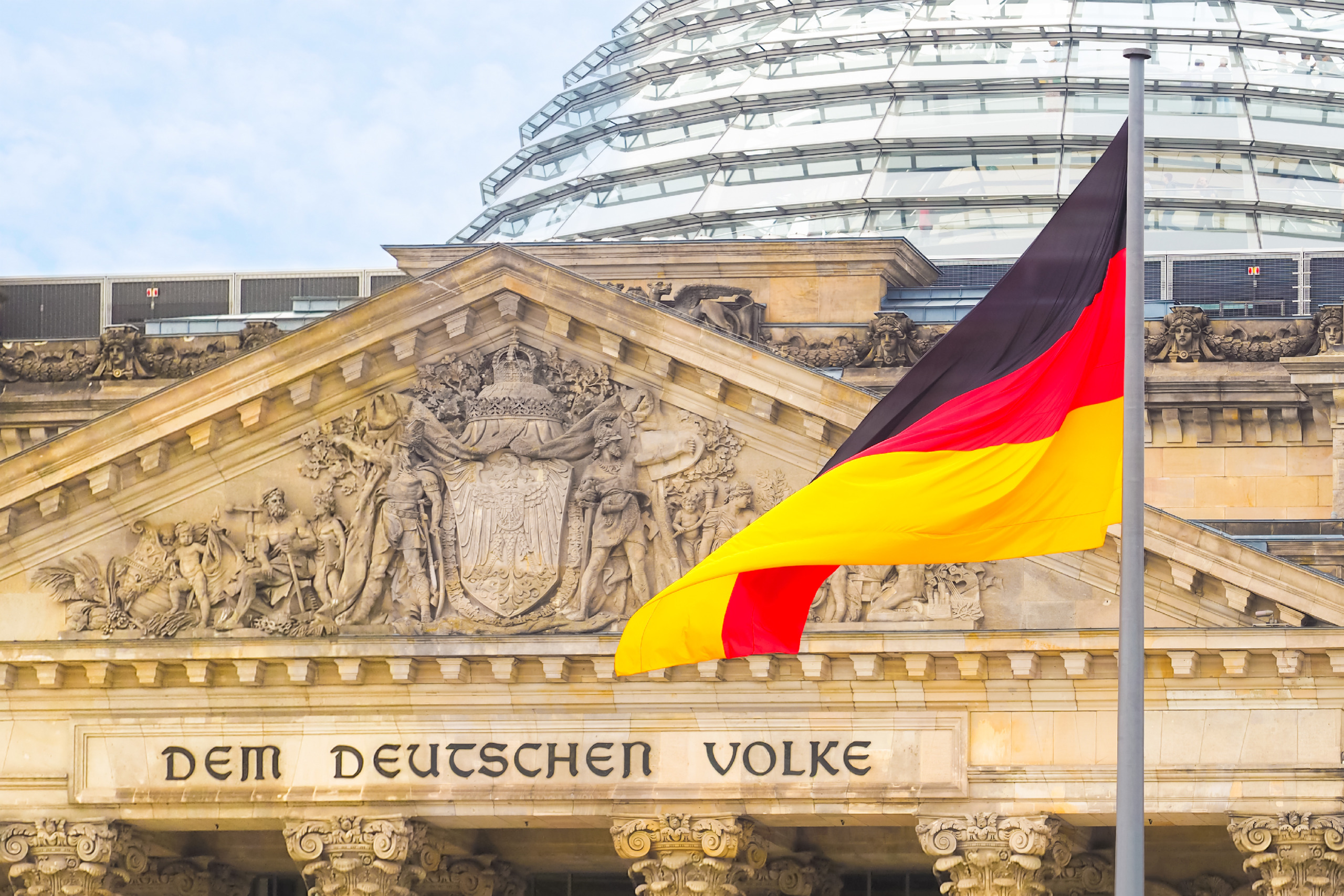
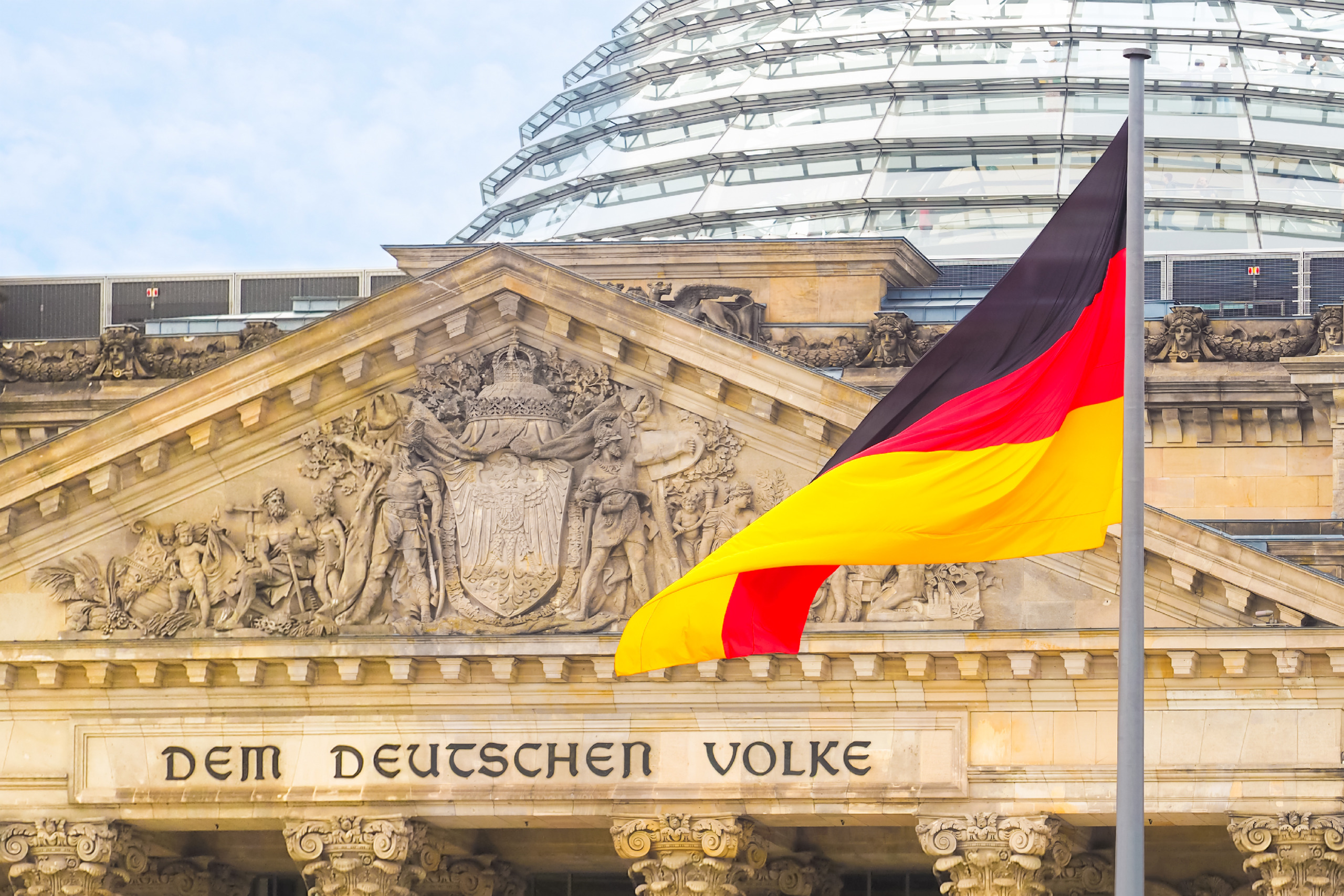
VDA6.3は、VDA6のパート3の略称。パート3なんで、パート1、2もあります。
全体のイメージ図
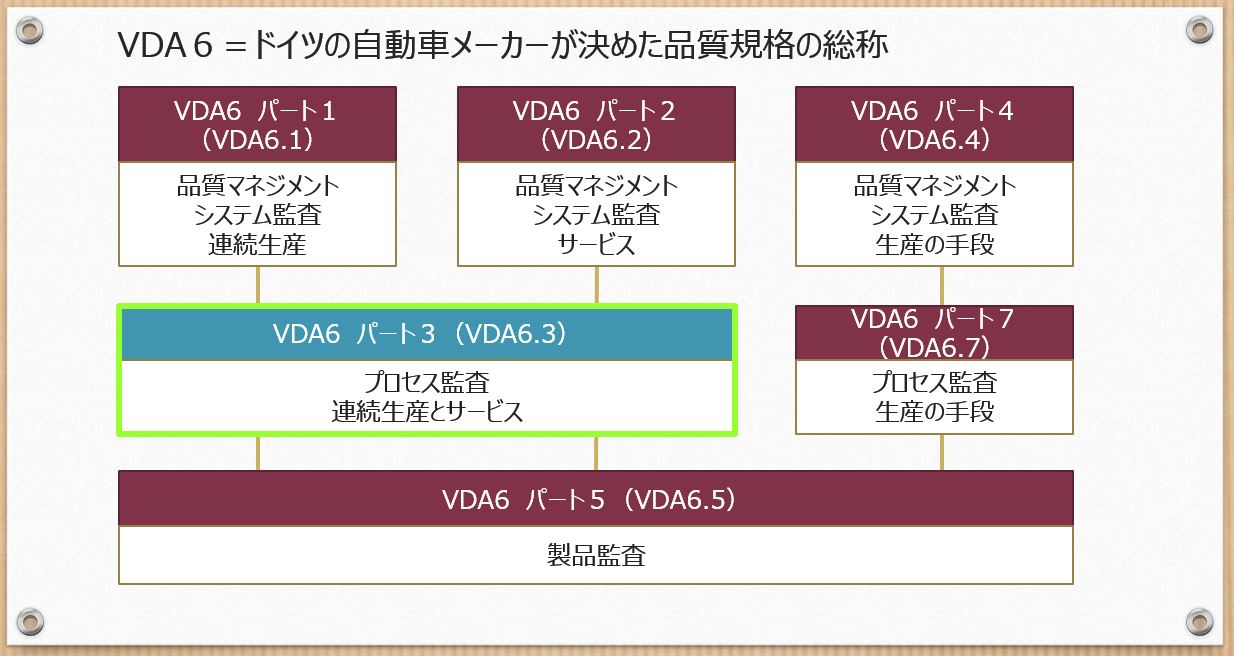
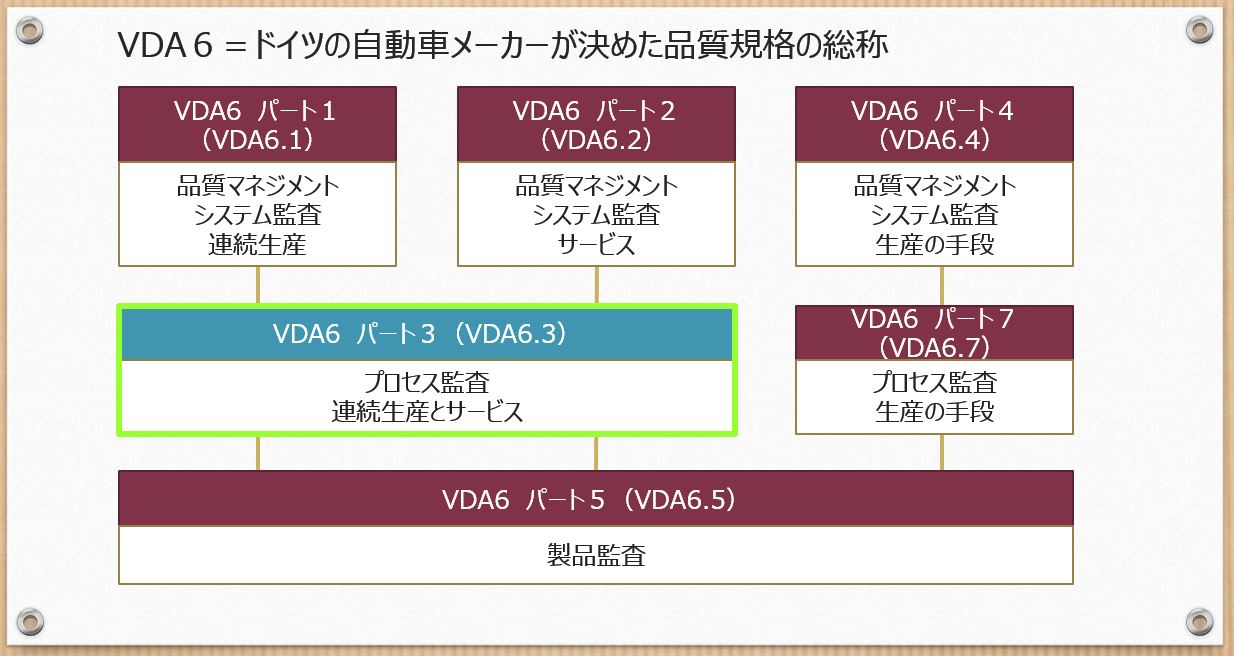
VDA6.1と6.2は、工場で製品を量産する前の審査です。
- VDA6.1
-
製品を開発する能力があるか?
- VDA6.2
-
その会社は安心して発注できるのか?
実際には、これまでの実績が考慮されたり、書類審査で終わるケースが多いです。
VDA6.3は、「いよいよ工場で製品を作れる段階になったんで、きちんと量産(連続生産)できるのかを現地の工場で確認します」という意味になります。
VDA6.3の要求事項って、なに?
VDA6.3の中にプロセスの要素と呼ばれるものが、7つあります。
「プロセス要素=大きな分類」みたいなもので、P1~P7で表現されます。
パート | 内容 |
---|---|
P1 | ポテンシャル分析 |
P2 | プロジェクトマネジメント |
P3 | 製品及びプロセス開発の計画 |
P4 | 製品及びプロセス開発の実施 |
P5 | サプライヤーマネジメント |
P6 | 生産プロセス分析 |
P7 | 顧客ケア、顧客満足、サービス |
タイトルだけだと、何をいってるか分からないんで、それぞれ説明します(^^;
P1:ポテンシャル分析
ポテンシャル分析は、自動車メーカーが新しく部品を購入しようとした場合に、その部品を作っている会社が安心できるか、問題ない会社なのかを評価します。
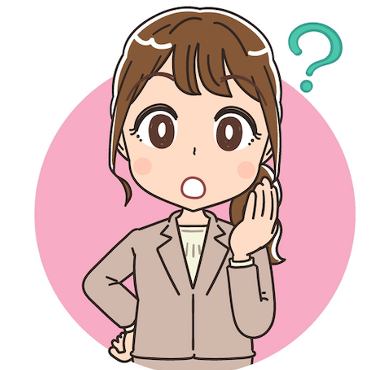
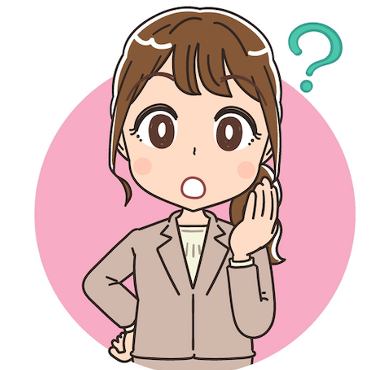
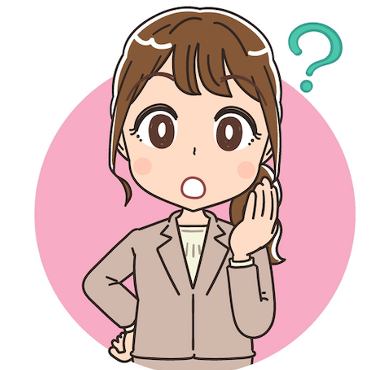
この会社って、本当に契約しても大丈夫なの?
という不安を取り除きます。
評価の方法は、専用のチェックシートの質問に自己診断で回答して、自動車メーカーに提出して判断してもらいます。自己診断の結果が悪いと、そもそも契約してもらえない仕組みになっています。
質問の内容は、この後にでてくるP2~P7までの内容を抜粋したもので、2020年10月時点だと、36項目の評価項目があります。なかなか大変^^;
この自己評価の結果で、その会社に製品を頼める実力(ポテンシャル)があるかを判断されます。これがポテンシャル分析のイメージです。
これが通らないと、そもそも工場の監査(VDA6.3)を受けることができません。
ポテンシャル分析の詳しい内容はこちらの記事で解説してます。
P2:プロジェクトマネジメント
プロジェクトマネジメント(P2)の中には7つの質問があって、P2.1~P2.7と表現されてます。質問の概要を簡単に書くと、
製品を作るための
P2.1 | ちゃんとした組織があるか? |
P2.2 | 材料や人員、設備は十分か? |
P2.3 | 生産のスケジュールは、顧客と合意してるか? |
P2.4 | 品質を保証する評価の計画はあるか? |
P2.5 | 材料・部品メーカーは、ちゃんとした所を使ってるか? |
P2.6 | 変更があった場合は、ちゃんと管理しているか? |
P2.7 | なにか問題が起こった場合、報告する仕組みはあるか? |
製品を設計、開発して、生産する前までの組織(プロジェクト)が機能しているかがポイントです。
P3:製品及びプロセス開発の計画
P3には、5つの質問があります。P3.1~P3.5と表現されます。
P3.1 | 製品を作る技術はあるか? |
P3.2 | この製品を作ることは、本当に可能か? |
P3.3 | 具体的な開発計画はあるか? |
P3.4 | 事故(クレーム)が起こった場合の対応を計画してるか? |
P3.5 | 人・材料・設備が十分に考慮されてるか? |
P3は「製品を作る上で必要なことを、具体的に計画しているか?」を確認する質問です。製品の開発段階で、十分に検討されてないと、良い製品はできません。
P4:製品及びプロセス開発の実施
P4には8つの質問があります。P3で作った計画を、具体的に実現していく段階です。
P4.1 | P3で計画したことが、きちんと実施されてるか? |
P4.2 | 製品を作るのに、必要な人は十分確保してるか? その人は作業をする資格を持っているか? |
P4.3 | 製品を作る装置は、使える状態になっているか? |
P4.4 | 製品の評価結果は、自動車メーカーの承認を得ているか? |
P4.5 | 製品開発のときに作ったFMEA、コントロールプランに基づいて、量産できる状態か? |
P4.6 | 製品の実力(パフォーマンス)を評価する方法は、量産と同じ条件で行われているか? |
P4.7 | クレーム品を分析して、対策・改善する能力があるか? |
P4.8 | 開発から量産に移行する方法が、整備されているか? |
実際に製品を作る(量産する)前に、全ての準備が整っているかを中心に確認されます。代表的なアウトプットは、工程FMEAとコントロールプランです。
FMEAとコントロールプランの詳しい解説はこちら
P5:サプライヤーマネジメント
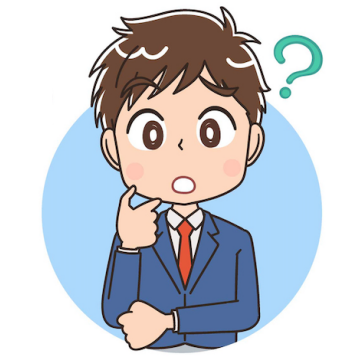
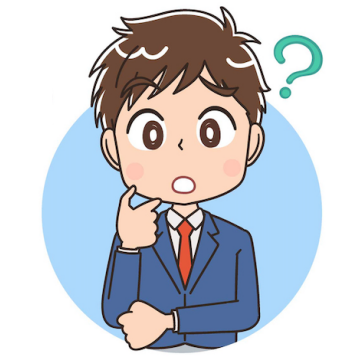
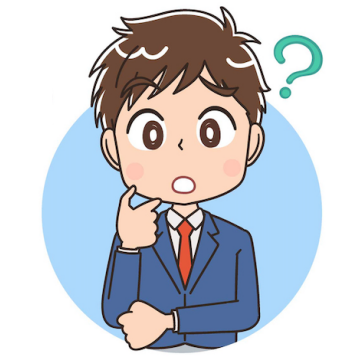
サプライヤーって、なに?
サプライヤーは、自分の会社から見て、材料や部品を購入する仕入先の会社です。ただ、どこを視点にするかで呼び方が変わってきます。
自動車メーカーから見ると、自分の会社がサプライヤー。自分の会社が購入している仕入先は、サブサプライヤーと呼ばれます。
図にすると、こんな感じ
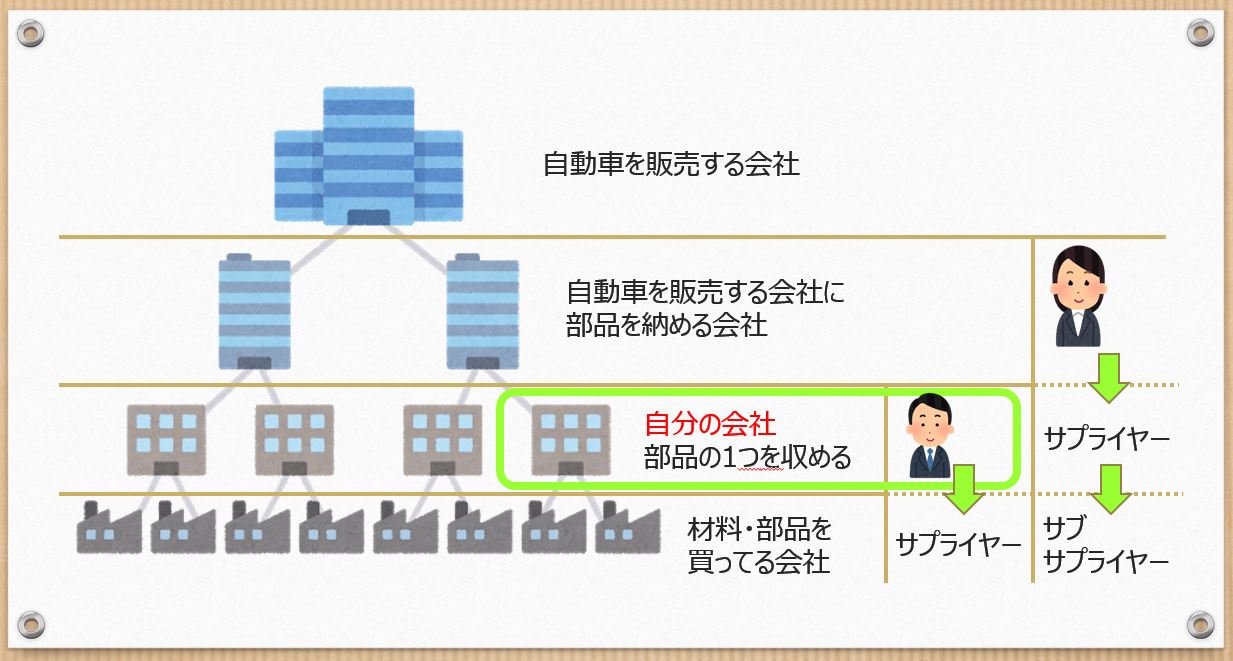
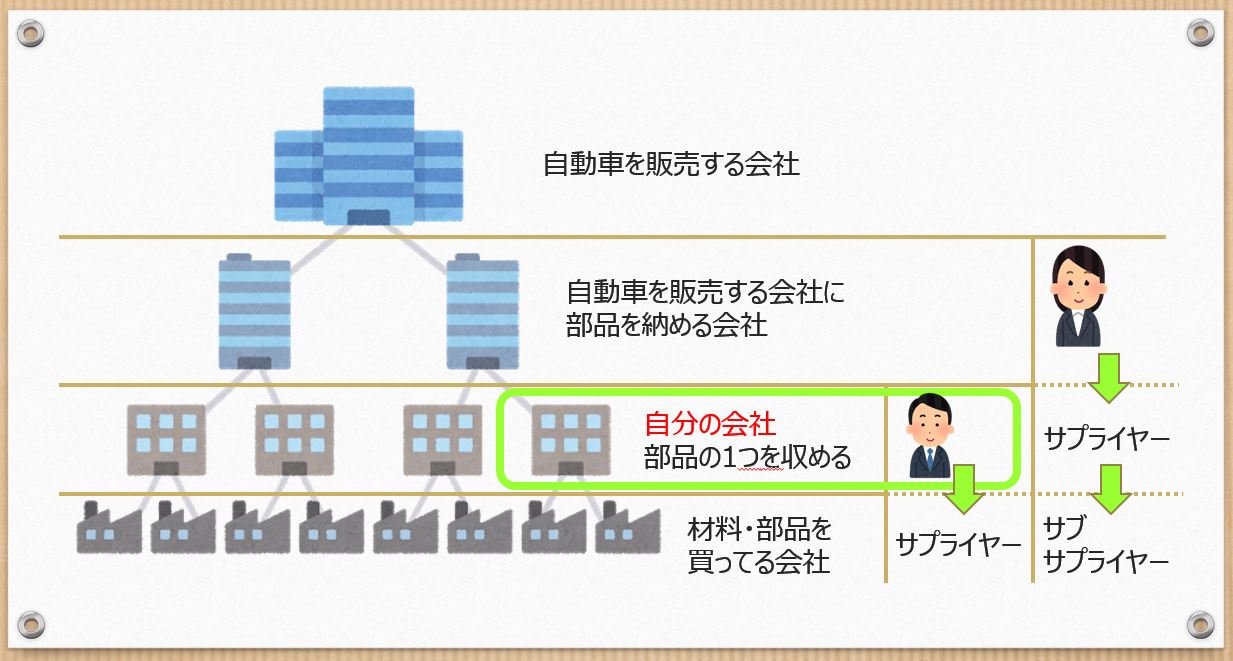
このP5は自分の会社から見て、仕入先(部品メーカや材料メーカ)の管理に関する質問です。
質問は全部で7つ。P5.1~P5.7まであります。
P5.1 | 品質に問題のない材料・部品メーカーを使っているか? |
P5.2 | 自動車メーカーが求めていることが、材料・部品メーカーに伝わっているか? |
P5.3 | 材料・部品メーカーに品質の目標があるか? |
P5.4 | 材料・部品の品質は問題ないことが保証されてるか? |
P5.5 | 購入する材料・部品の品質は、チェックされているか? |
P5.6 | 購入した材料・部品は、きちんと受入れて、保管されているか? |
P5.7 | 材料・部品を管理する人は、その資格を持っているか? |
材料・部品メーカーを信用して購入するだけじゃ、ダメってことですね^^
材料・部品メーカーを指導して、良い品質を保つ活動をしなさいって言われてます。
P6:生産プロセス分析
このP6の質問が、主に工場監査で確認される内容です。
P6.1~P6.6まで分類があって、その中にさらに細かな質問があります。
P6.1 | プロセスには、何が入るのか?(インプット) |
P6.2 | 生産するための手段は、管理されているか? |
P6.3 | 生産するための人員は、確保されているか? |
P6.4 | 生産するための設備は、整備されているか? |
P6.5 | プロセスは、機能しているか? |
P6.6 | プロセスは、何を生み出すのか?(アウトプット) |
このP6.1~6.6の分類は、タートル分析と同じ内容になっています。
タートル分析の詳しい内容はこちらの記事で解説してます。
P7:顧客ケア、顧客満足、サービス
P7は、製品を納品した後のアフターサービスに関するものです。
納品した製品が壊れたり、機能しなかったりした場合のクレーム対応がメインになります。P7.1~7.5までの5つの質問があります。
P7.1 | 自動車メーカーが求めていることが満足できるか? |
P7.2 | 自動車メーカーが求めているサービスを保証できるか? |
P7.3 | 部品を安定して、供給することができるか? |
P7.4 | クレームが起こった場合、原因が追求されて、対策が効果的に実施できるか? |
P7.5 | サービスを担当する人は、その資格を持っているか? |
自動車メーカーから見ると、問題が起こったときのクレーム対応が1番気になるポイントです。
自動車部品だと欠陥が分かった段階で、リコールなどの法的制度があるので、きちんと対応できる体制が必要になります。
まとめ:VDA6.3ではP1〜P7の質問を審査
VDA6.3監査で行われること
- P1:ポテンシャル分析
-
- 自己診断の結果で、製品を開発、量産する能力のある会社か?を判断されます。
- P2:プロジェクトマネジメント
-
- 組織的な製品を開発、量産する体制があるか?の確認
- P3:製品及びプロセス開発の計画
-
- 製品を開発する十分な計画を持っているか?
- P4:製品及びプロセス開発の実施
-
計画したものを実行できる能力があるか?
- P5:サプライヤーマネジメント
-
材料・部品の購入先を管理できているか?
- P6:生産プロセス分析
-
量産する能力があるか?
- P7:顧客ケア、顧客満足、サービス
-
クレームを処理する能力があるか?
VDA6.3の監査は、製品を受注するところから、設計、開発、量産、アフターサービスに至るまでの一連の流れを全て確認されます。
多くの時間をかけて、じっくり監査されるので、かなり大変です^^;
逆に、ここまでして安全な自動車を作ろうって言う意気込みも感じます。
自動車が故障するとすごく困ります。そうならないように1つ1つの部品の品質をあげる活動が、VDA6の考え方です。
大変な監査ですが、頑張って乗り切りましょう。
最後までお付き合い、ありがとうございました。m(_ _)m