品質管理の仕事をしていると「QC7つ道具」という言葉に出会います。昔からある現場を管理・改善するツールです。
- パレート図
- ヒストグラム
- 特性要因図
- チェックシート
- 管理図
- 散布図
- グラフ
- 層別
全部で8個ありますが、層別は後から追加されました。①〜⑦は、図や表などのツールですが、層別だけが考え方です。
でも、25年以上製造現場の品質管理をしてきましたが、QC7つ道具を意識して使ったことはありません(^^;
普段の仕事に溶け込んでいたり、まったく使わなかったりです。
QC検定にも出題される重要な考え方ですが、現場で実践するときには、もう少し深掘りが必要。
この記事では、僕の経験から現場での具体的な使い方を解説します。
QC検定の2級や3級で基礎は勉強できますが、「実際に現場でどうやって使うの?」という疑問に答えていきます。基礎だけだと、現場では使えなかったりします。
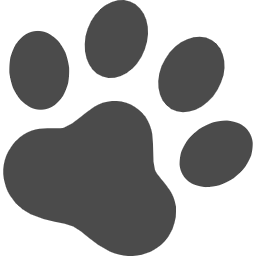
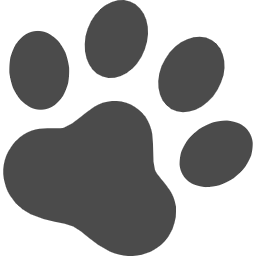
- QC7つ道具の使い方がいまいち分からない人
- これから品質管理の仕事をする人
- 現場の品質管理を1~2年担当している人
QC7つ道具が今の現場で使えるか?
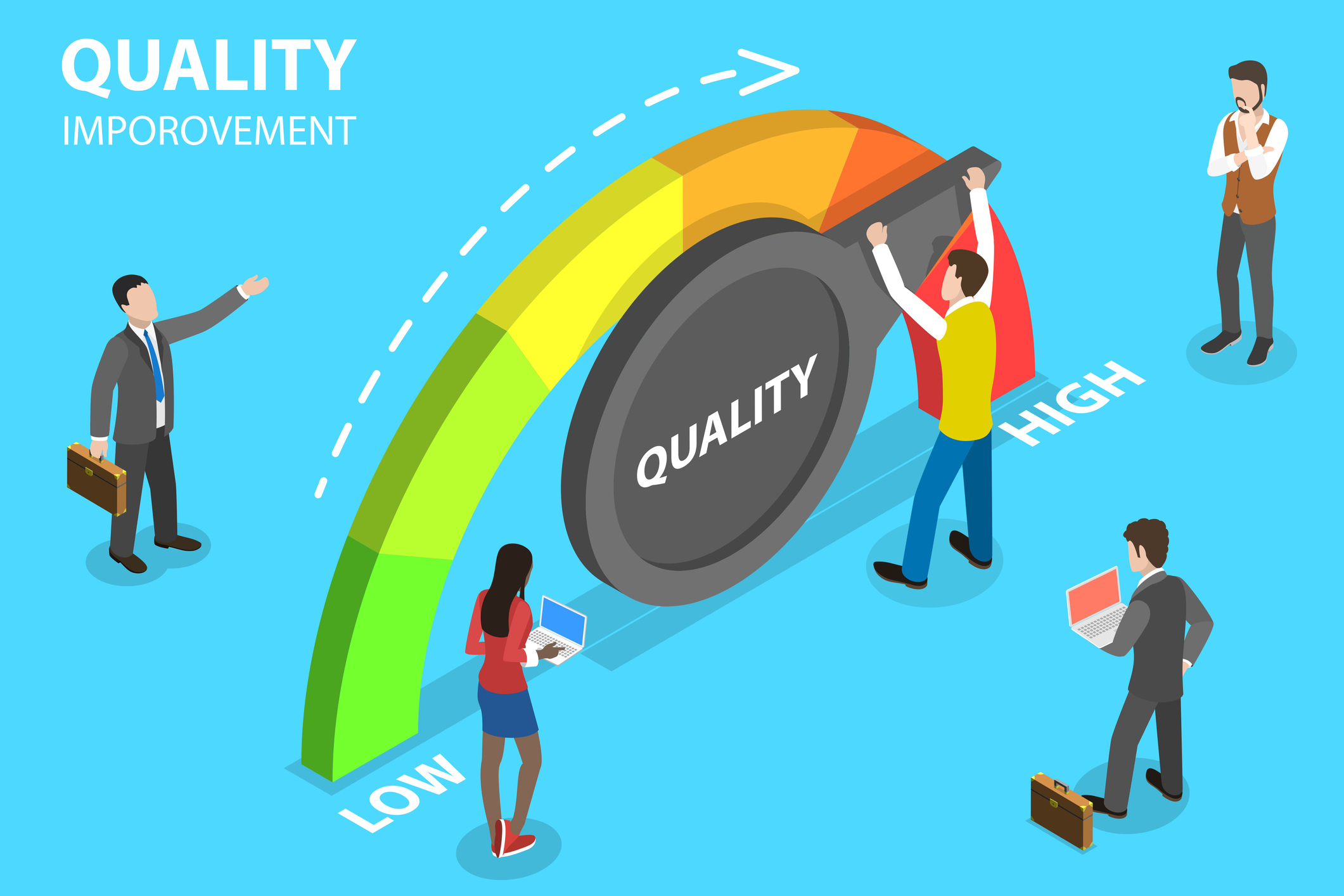
QC7つ道具は、すごい昔からある考え方のため、いま運用しようとすると使い方が少し変わります。Excelや分析ツールの発達で、より簡単にデータが解析できるようになった影響です。
パレート図は知らなくても、Excelのグラフで棒グラフを大きい順番に並べることは、誰でも簡単にできたりします。
QC7つ道具を使う目的は、本質を見極めて、効率よく改善を行うこと。7つ道具の形じゃなくても、結果が伴っていれば問題ありません。
QC7つ道具の現場運用
No | 7つ道具 | 実際に使ってみた感想 | 今でも使える? |
---|---|---|---|
1 | パレート図 | Excelのグラフで問題なし | |
2 | ヒストグラム | Excelのグラフで問題なし | |
3 | 特性要因図 | FTAの方が使える | |
4 | グラフ | 普通に使っている | |
5 | チェックシート | 普通に使っている | |
6 | 管理図 | SPC管理にグレードアップ | |
7 | 散布図 | 原因究明に使える | |
8 | 層別 | 原因究明に使える |
上から3つは、ほぼ使わないですね^^;
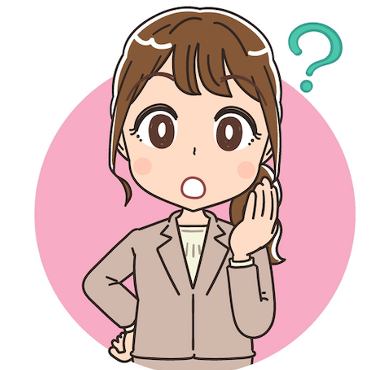
じゃあ、実際にどうやって使うの?
具体的な例を出して、使い方を説明していきます。
テーマ
いきなりですが、「いちごの収穫」をテーマに考えてみます。(いちご好きなんで^^)
収穫した20個のいちごに、大きさ・見た目・甘さのデータを付けてみます。
パレート図の実践
パレート図の目的は、不具合の改善を行う場合に、どこから攻めていくかを判断する材料に使います。
いちごの不具合を考えると「出荷できないもの=キズがある、色が白い、小さい、甘くない」です。
Excelで不具合の表に割合を入れて、棒グラフ+折れ線グラフを作っただけです。これをパレート図と意識して作っている人の方が少ないかも知れません。
本当のパレート図の形は少し違いますが、実務に支障はありません。逆にパレート図の方が見にくかったりします。
Excelで作った棒グラフを円グラフに変えてみます。場合によっては、円グラフの方がわかりやすいこともあります。
大切なことはパレート図の様式にこだわらず、どの不具合モードが多いのか?という目的を達成すること。
パレート図を使うこと自体には、意味がありません。考え方がしっかりしてれば、なんでもOKです^^
ヒストグラムの実践
ヒストグラムは、「何が何個あるか?」をグラフにしたものです。いちごの大きさを基準にして、何cmのものが何個あるかを調べてみます。
5cmのいちごが6個で、全体の30%を占めてることが分かります。
昔は集計に時間が掛かりましたが、いまはExcelのピボットテーブルで簡単に表が作れます。その表を棒グラフにすれば完成です。
もう1つ、いちごの甘さを基準にグラフを作ってみます。
糖度13が25%と1番多いです。糖度12~15に大きな差はなくて、全体の75%を占めていることも分かります。
ヒストグラムの目的は、データがどんな分布をしているかを把握することです。
Excelで表を作って棒グラフにすることで、十分目的は達成されます。ヒストグラムという言葉は知らなくても、普段から何気なく使ってると思います^^
特性要因図の実践
特性要因図は、問題が発生した場合の原因究明に使うツールです。だた僕はあまり好きじゃありません(^^;
要因を、魚の骨に見立てた大きな骨・中位の骨・小骨と枝分かれした場所に書き出して使います。
しかし、重要な小骨がいくほど、書く所が小さくなって、自分が何をしてるのか分からなくなります。
「いちごが白い」という問題に対して、何で白いんだろう?の原因を探るため、魚の骨を書いてみました。骨を書くだけで用紙いっぱいで、文字を書き込む気になりません。
これに変わる有効的な手段が、FTA(Fault Tree Analysis=故障の木解析)です。
FTAだと、原因の要素を何個書き出してもExcelの行が増えるだけなので、深堀りしやすいツール。僕はこっちの方がやりやすくて好きです^^
FTAの詳しい使い方はこちらの記事で解説してます。
チェックシートの実践
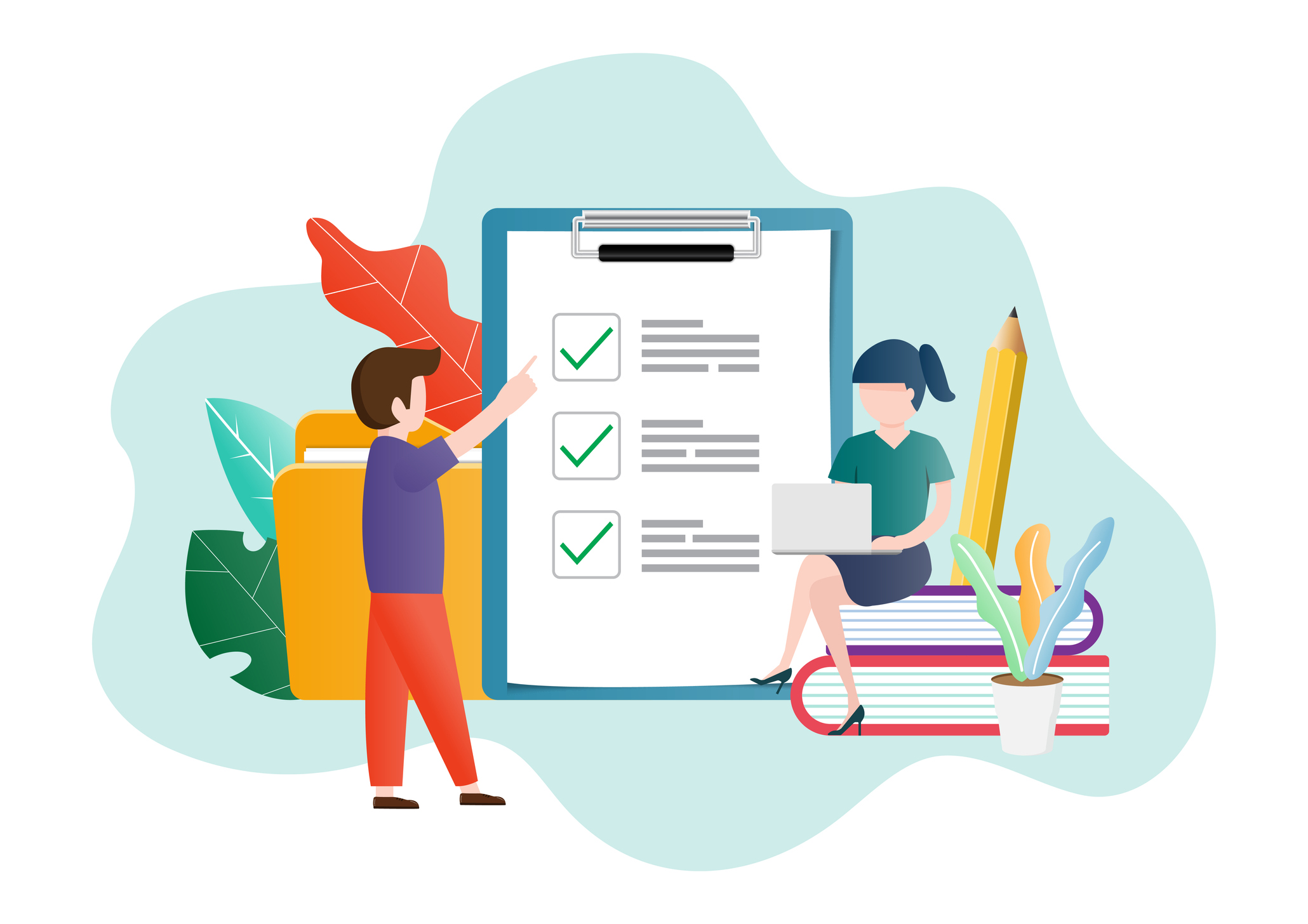
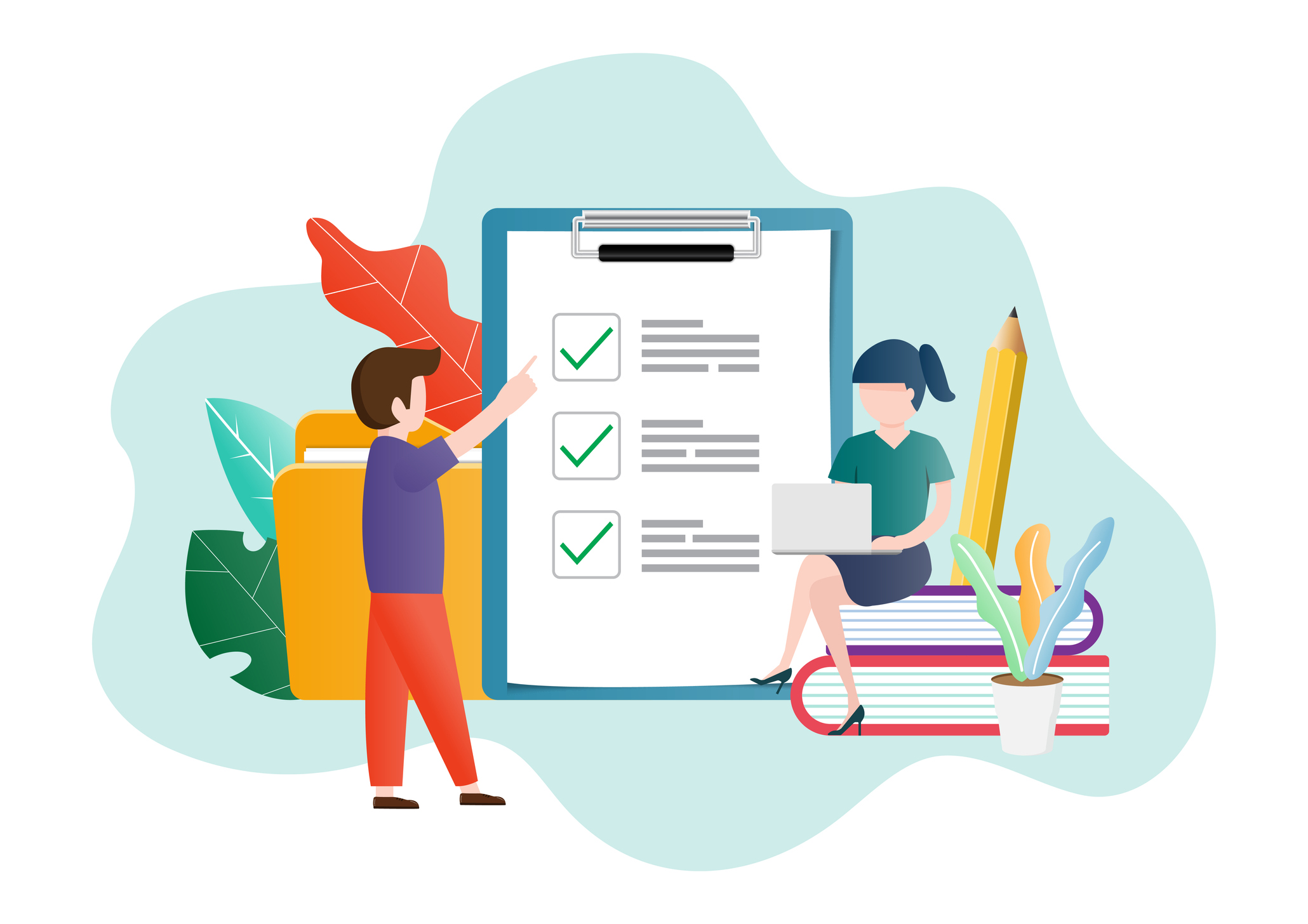
現場で使うチェックシートは、大きく2種類あります。
- 記録用のチェックシート
- 点検用のチェックシート
記録用のチェックシート
何かを測定した結果や検査した結果を記入するチェックシートです。結果を書くだけですが、これも立派なチェックシート。
でも、実際使おうとすると少し情報が足りませんので、少し工夫して
ポイントは測定・検査した結果を記入することで、良いものか悪いものかを判定できるようにする点です。
また記録として残すので、後から調べることができるように検査する人や日付が分かるようにすることも大切です。
点検用のチェックシート
あらかじめ実施することを決めて、その通り実施したかを記録するチェックシートです。主に設備の点検や日常の清掃に使用します。簡単な例ですが、こんな感じです。
ポイントは、内容の欄を具体的にすることです。誰が、どこを・何を使って・何をする、など書いていることをするだけで良いよう作ります。
管理図の実践
管理図は、現場目線で見ると折れ線グラフの1つと思って大丈夫です。いちごの大きさを1個目から順番に20個目まで折れ線グラフを書いてみます。
ここに大きさの規格を入れてみます。小さくても美味しくないし、大きすぎても大味です。
美味しいいちごを届けるために、3~8cmの大きさだけを出荷することにします。
13個目のいちごが小さくて出荷できないことが分かります。
チェックシートに記録した測定結果をグラフで視覚化したものが管理図です。上下の赤い線は、管理線と呼ばれます。
2個目や6個目が線の上に点があります。オンラインと呼びますが、その会社で取り決めがなければ、一般的にオンラインは合格(OK)で問題ありません。
最近は、この管理線の数字に過去のデータから統計的に計算したものを使う管理図が浸透してきています。SPCと呼ばれる管理図で、工程能力の考え方を使った3σ管理が有効です。
SPCの詳しい考え方は、こちらで解説してます。
散布図の実践
散布図は、2つの要素を同時にグラフ上に表すことで、その関係性を理解するのに役立ちます。いちごの大きさと甘さに関係があるか見てみましょう。
小粒のいちごの甘さが低くて、4~5cmが1番甘い。それ以上大きくなると、あまり変わらないことが分かります。
この結果だと、3cmになると甘さ(糖度)が10を下回ります。安定して甘いいちごを出荷するなら、大きさの規格を3→4cmに引き上げる必要があります。
ポイントは2つ要素にどんな関係性があるかを見極めることです。
点の集合体を遠くから見て、線や曲線が引ければ何かしらの関係があると考えられます。関係性があれば、更にそこから深く調査するヒントになります。
散布図は、現場の管理で使うよりも改善や原因究明に広く使われています。
グラフの実践
グラフは、QC7つ道具のベースです。これまでのパレート図・ヒストグラム・管理図・散布図は、すべてグラフ。
棒グラフ、円グラフ、折れ線グラフ、散布図は、すべてExcelで作成できます。Excelの登場は、QC7つ道具の使い方を変えて、現場改善の効率を大きく向上させました。
層別の実践
層別は、不具合が発生した場合の原因究明の手段として使われます。
QC7つ道具に特性要因図がありますが、その大骨・中骨になる項目1つ1つの階層です(1段ずつ下におりていくイメージ)
大骨には、常に5M1Eを当てはめて考えます。
5M1E
5M1E | 具体的なアイテム |
---|---|
人 | 経験年数・男性/女性・疲れ具合・作業した時間・年齢など |
装置・設備 | 号機・機種・ライン・使用年数・メンテナンス・故障・治工具など |
材料 | 成分・特性・材料メーカー・製造時期・劣化・使用時間など |
方法 | 条件・作業の方法・加工温度・加工圧力・加工方式など |
測定・検査 | 測定機器・検査機器・校正など |
環境 | エリアの温度・湿度・照明・水質・清浄度など |
5M1Eの詳しい内容は、こちらの記事で解説してます。
まとめ:QC7つ道具を現場で実践
QC7つ道具は、そのままでは使いにくい面もありますが、考え方は大変参考になります。Excelを上手に活用して、現場管理・現場改善に役立てましょう!
- パレート図
-
どの不具合が1番多いのかを知ることが目的です。Excelの棒グラフ・円グラフを活用しましょう。
- ヒストグラム
-
データがどんな分布をしているか把握することが目的です。Excelの棒グラフを活用しましょう。
- 特性要因図
-
不具合の原因究明に層別で深掘りしていくツールです。実践ではFTAを使いましょう。
- チェックシート
-
現場の人がチェックシートに書かれていることをするだけで良いように作りましょう。
- 管理図
-
管理線に3σ管理を適用することが求められています。SPCを理解して昇格させましょう。
- 散布図
-
2つの要素に関係性があるかを視覚化できます。点に線や曲線を引いてみましょう。
- グラフ
-
今ではQC7つ道具のベースになっています。それぞれのグラフを使いこなしましょう。
- 層別
-
不具合が発生した原因を追求していく考え方です。5M1Eを切り口に1つ1つ細分化していきましょう。
本記事は以上となります。
最後まで読んで頂き、ありがとうございました。<(_ _)>
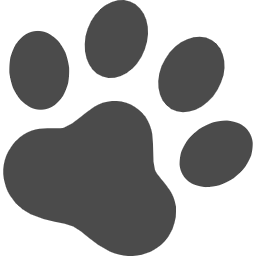
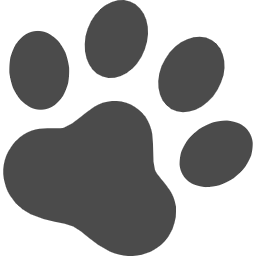
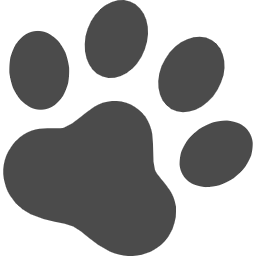
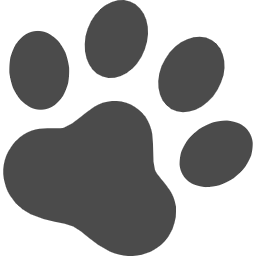