製造の現場で品質の事故やクレームを受け付けたとき、原因を究明する手法にFTA(Fault Tree Analysis)があります。
クレームの報告書で原因調査の説明として、このFTAやフィッシュボーンがよく使われます。
でも、ネット検索しても現場で使えそうなFTAの具体的なやり方が見当たらない。。
- FTAって、どうやるの?
- 何から書けばいいの?
- 使い方がよくわかんないんだけど・・
この記事では、そんな疑問に答えていきます^^
製造現場で25年ほど品質管理の仕事をしてきました。理論的な考え方より、現場で使ってきた実践的な考え方を紹介します。
それは本来の考え方・使い方じゃないよ!って箇所もあるかも知れません。
でも、ツールはあくまで手法なので、目的にたどり着ければOKだと思ってます。<(_ _)>
- クレームの報告書をよく作成する人
- FTAをこれから使おうと思っている人
- FTAを使っているけど、どうもしっくりこない人
YouTubeの解説動画はこちら
FTAの考え方
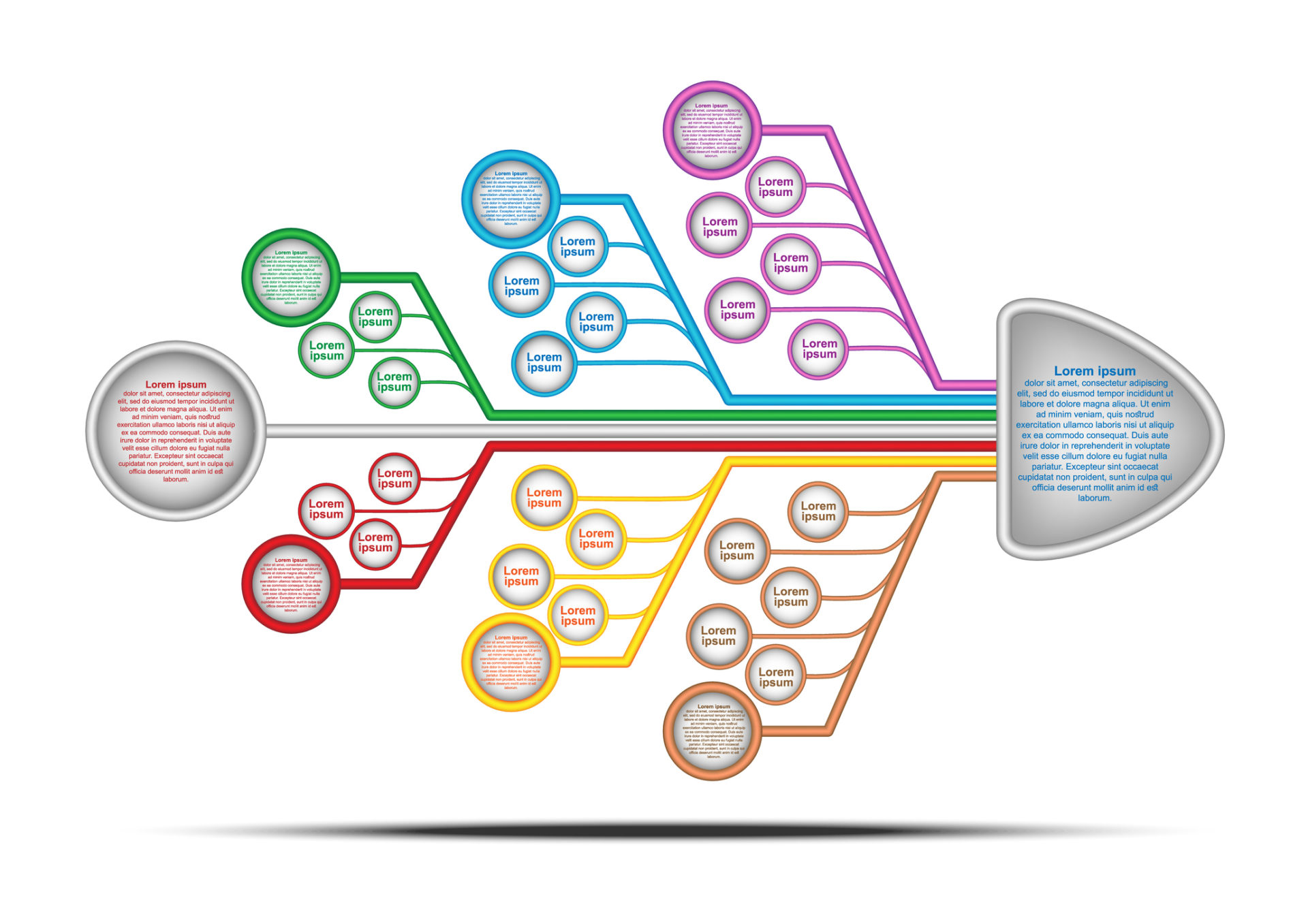
FTAは、何かトラブルが発生したことを起点にスタートします。
似たものに特性要因図(フィッシュボーン)がありますが、考え方は同じで見た目が違うだけと思って問題ありません。
僕も最初から特性要因図で原因究明をしたことがありません。
FTAを理解していれば、特性要因図は形を変えるだけなので、気にする必要はないです。
経験上の少し偏った意見ですが、海外のメーカーはフィッシュボーンが好きで、日本のメーカーはFTAが好きな気がします。
海外のレポートにフィッシュボーンが必要で、書き換えたことが何度かあります。文化の違いかも知れません(^^;;
FTAとFMEAの違い
少し余談ですが、車の部品を扱っているとFMEAという言葉がよくでてきます。
FMEAは、トラブルが起きる前に事前にリスクがないかを解析するツールです。FMEAが完成されていれば、FTAを考える必要はありません。
「FTAをする」ということは「トラブルが起こった」ことになるので、FMEAが十分でなかった!もしくはFMEAでリスクが高いことはあらかじめ分かっていた!ことを意味します。
僕は、FMEAが最も現場管理に使えるツールだと考えています。FMEAを既に作成しているのであれば、FTAを行う前にFMEAを確認してみて欲しいです。
FTAとFMEAにはアプローチする順番が違うだけで、密接な関係があります。
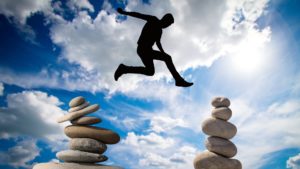
FTAのフォーマット
フォーマットは、Excelで作るのが使いやすいです。一般的なフォーマットはこんな感じです。
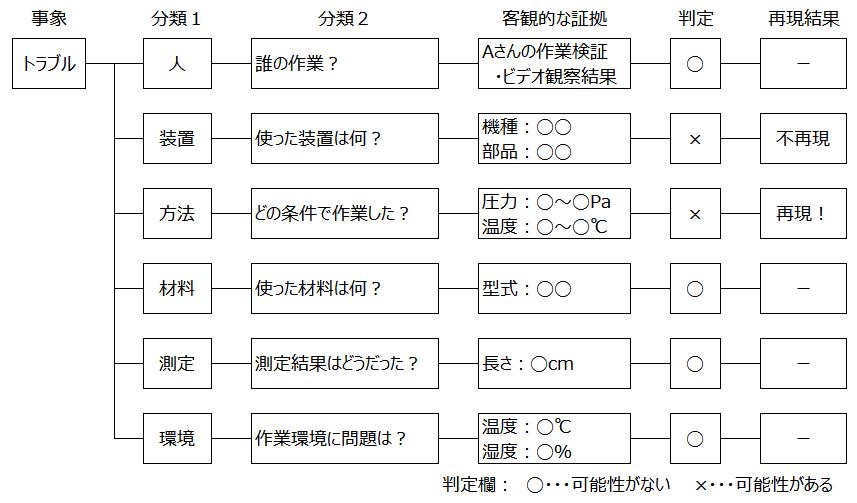
分類1には、5M1Eをベースにした言葉を入れればOKです。FTAは、分類2にどれだけの要因を書き出せるかがポイントです。
5M1Eについての詳しい解説はこちらの記事を参考にしてください。
FTAの進め方
FTAの進め方は、7つのステップで行います。
- FTAチーム・リーダーの選定
- トラブルの原因なりそうな項目を思いつく限り並べる
- 抽出した要因を調査する
- 1次判定する
- 再現実験を行う
- 原因の特定
- どれも再現しない
それぞれ説明します。
トラブルが発生した場合、問題解決のチームを作ります。
メンバーは、会社組織の各部署から経験のある人を選定しましょう。その分野にどれだけ多くの知識を持っているかが大切です。
リーダーがいないと、意思決定に時間がかかって、間違った方向に進んでしまうことがあります。経験豊富なリーダがいるとすんなり進んでいきます^^
フォーマットの分類2の欄です。
「これは大丈夫だろう!」という考えは一旦やめて、少しでも原因に関係しそうなものは書き出します。
「人」の部分は現場に詳しい人、「装置」の部分は機械に詳しい人みたいに役割を分担するとスムーズです。
最終的にはメンバー全員でレビューしますので、思いつくまま全てあげましょう。
1つの要因に対して、客観的な証拠になるデータを調査します。
調査結果は、数値や記録と具体的なものが必要です。人の証言や想像だと要因を消せる証拠にはならないので注意します。
トラブルの原因ではないという具体的な証拠がある場合に「◯」を入れます。
例えば「規格10±2cmに対して、調査結果10.5cmだったので問題なし」などです。
証拠が不十分だったり、NGだった項目が対象(×)として残します。
会社の報告書の書き方によって、◯と×の意味が入れ替わることがありますので、その点は注意をお願いします<(_ _)>
可能性が残った項目(×)に対して、再現させて、同じトラブルが発生するか検証します。
再現しなければ、原因じゃない可能性がでてきます。
同じトラブルが再現すれば、その項目が原因で間違いありません。対策に移りましょう!
まれに再現しないこともあります。
その場合、大半は「分類2」の抽出不足です。もう1度、原因の洗い出しに戻ってしまいます・・・、うーん、大変^^;
原因にたどり着けない場合の対処法
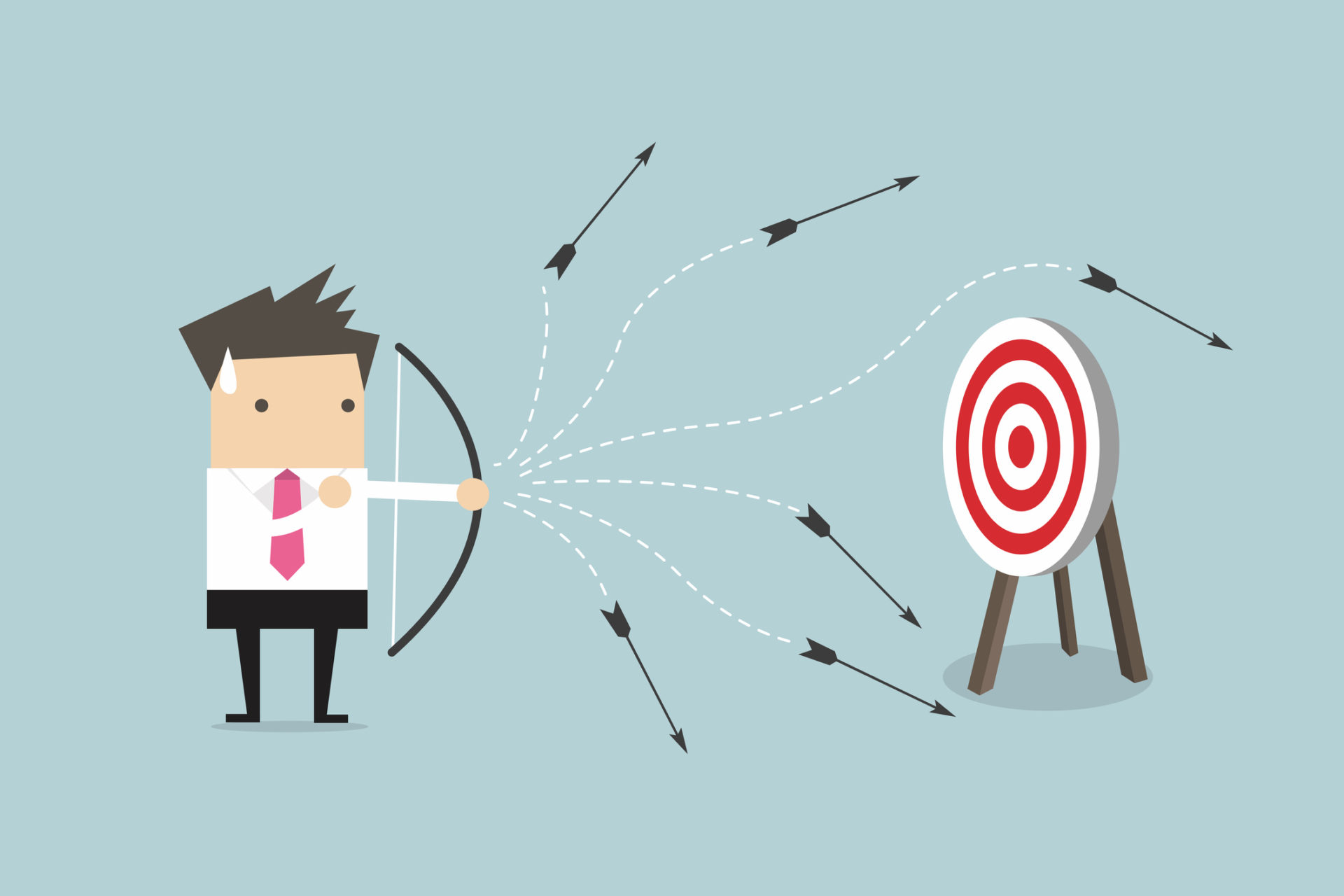
どうやってもトラブルが再現せずに息詰まることがあるかも知れません。
その場合、時間はかかりますが、現場レベルでのFMEA作成が結果的に近道です。
既にFMEAがある場合は、FMEAを持って現場作業を1つ1つチェックしていく作業をします。FMEAに抜けや漏れが必ずあるはずです。
FMEAの作成方法は別の記事を参照下さい。
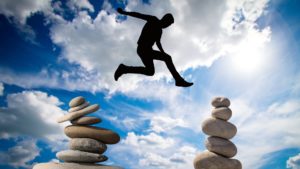
FMEAに反映
トラブルの要因・対策内容は、全てFMEAに反映します。
トラブルの対策が、発生対策なのか?流出対策なのか?色々な改善施策があると思います。FMEAはその全てを網羅することができます。
FMEAはトラブルを積み上げることで精度があがり、会社の財産になります。今回のトラブルを教材して、FMEAを見直すことで再発を予防できます。
FTAに関する書籍は数少ないです。初心者向けではありませんが、以下の書籍を読んでみるのも参考になります。
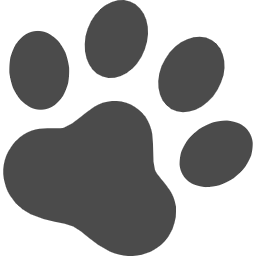
ちょっと高いので、近所に図書館があれば探してみて下さい(^^;
本記事は以上となります。最後までお付き合い、ありがとうございました。
それでは、またっ!m(_ _)m