工程管理の兄弟にあたる工程改善。日本のモノ作りの強みとして海外でも「KAIZEN」という呼び方で広く知られてます。
安定して良いモノを作るためには、「管理」を続けていけば問題ありません^^
でも「管理」だけだと、それ以上のモノは作れません。安定だけだと、競合他社に負けてしまいます。
そこで大切なのが「改善」です。
- 今の管理を良い方向に改善していく
- 改善したことを管理していく
このサイクルを続けていくことで、常に成長していくことができます^^
今では当たり前に使われてる「改善(KAIZEN)」という言葉ですが、これから改善に取り組む方に向けて改善の方法を具体的に解説していきます。
- これから改善しようと思ってる人
- 改善ワークが上手くいなかい人
- 改善がマンネリ化してきた人
改善(KAIZEN)の方法
改善の方法は、5つのステップで構成されてます。
- 改善の目的は何か?
- 何を改善するのか?
- 分析する
- 改善してみる
- 検証する
それぞれ解説していきます。
目的は何か?
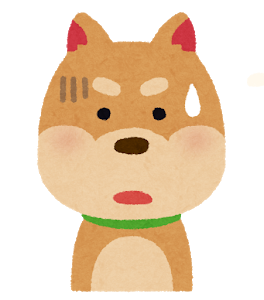
って思われるかも知れませんが、改善という意識が先走るあまり、目的を見失うことはよくあります(^^;
改善に行き詰まったり、悩んだ時は、
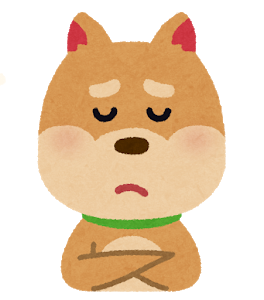
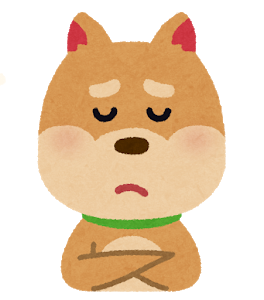
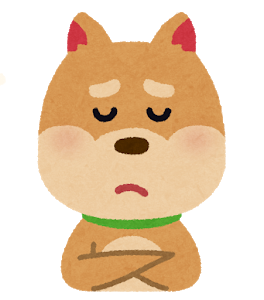
と自問自答してみると、結構モヤモヤが晴れたり、初心に帰ることができます。
具体的に目的をはっきりさせる方法は、まず会社の方針を思い出すことです。個人でも、会社でも、仕事をするための方針や目標はあると思います。
例えば、方針が
- どこよりも安い
- どこよりも早い(速い)
- どこよりも品質が良い
その場合の改善目的は、下の3つになります。
- コストを抑える
- つくる時間を短くする
- 不良品を減らす
何をするべきかが、はっきりしますよね。
会社は早く作りたいのに、不良品の改善をしていても、方向性が合いません。改善してることは悪くありませんが、まわりの協力を得られなかったり、改善の結果が評価されなかったりします。
ゴールが決まってないと、どこに走っていけば良いか分かりません。ゴールのない迷路ほどツライものはありません。迷走してるだけになってしまいます(^^;
方針や目標を見て、改善の目的(ゴール)をしっかり作ります。
何を改善するのか?
ゴールが決まれば、次はどのコースを走るかを決めます。改善の対象を決める作業です。
はっきりさせる対象は、「指標」と「工程」の2つです。
指標は、単位のことです。
- 安いの単位 → 円(¥)
- はやいの単位 → 時間(min、hr、日)
- 品質の単位 → 歩留り、不良率(%、ppm)
的はずれな単位だと、分析や検証がうまくできなくなります。
ただ「安く作る」という目標に、歩留りを上げる単位(%)を使うことがあります。
不良品が減れば良品が増えて「利益率が上がる」→「単価を抑える」→結果「安くなる」という考え方です。
間違っていませんが、注意が必要です。
単純に安い(円)を改善することと、歩留り(%)を改善するのでは、アプローチの方法が変わってきます。
「品質を良くした結果、コストを下げることができた」のと、「直接製品の単価を下げる」ことは違います。
会社の方針や考え方と照らし合わせて、間違っていないか確認しましょう。
もう一つの対象は、「工程」です。工程は、いくつかに分割された作業やグループです。モノ作りは、いくつかの工程、作業に分割されてます。
どの工程、どの作業を改善するのかを、はっきりさせます。
- コストがかかってる工程はどこか?
- 時間がかかってる作業はどこか?
- 不良の多い工程はどこか?
問題がない工程を改善しても、効果は得られません。ネックと呼ばれる工程を見つけて、改善の対象にすることが重要です。
そのために、定めた指標でしっかりした分析を行います。
分析する
データを集計して、グラフにして見える化します。工程と単位があれば、グラフ化は簡単です。例えば、
1つの商品を作るのに「C工程」が1番時間がかかってることが、すぐ分かります。
1つの商品は1個じゃない場合も多いです。分析する場合、その工場やラインで流すときの平均的な数量が良いです。
- 1,000個を1つの単位としてる場合は、1,000個
- バラバラな数量を1つの単位としてる場合は、その平均値
最もよく作業する1つの数量グループで分析しないと効果が得られないことがあります。
C工程がネックだと分かっていても、改善が難しい場合もあります。そのとき、次に悪いE工程を対象にしたくなります。
でも、E工程を改善しても、全体的に見たら商品を作る時間は大きく変わりません。C工程から出てくる商品の量は変わらないので、DとE工程の暇な時間が増えるだけです。
これが、改善効果があると思ってるのに、全体的な成果がでない原因です。
C工程がネックなのは分かりました。次は、C工程の中身を分析します。
③番目の作業に1番時間がかかってることがわかります。
実際に作業③を見て、どこに問題があるのかをはっきりさせます。
分析は、大きなところから、改善の対象を徐々に絞っていく、具体的にする作業です
改善してみる
分析して改善する対象の工程、作業は分かりました。あとは改善するだけです。
ここで心がけるポイントは、取り敢えずやってみるということです。改善プランは思いついても、やってみないと実際のところは分かりません。
ダメ元でやってみる行動力がないと、なかなか進みません。
「失敗は、成功の母」という言葉もあります^^
商品や製品の安全には十分配慮する必要があります。良いと思った改善が、思わぬ事故や不良をまねくことも考えられます。
会社だと、まわりの人とよく会話してから取り組むことが大切です。
検証する
改善の効果を確かめる作業です。
分析で行った方法と同じやり方でグラフを作ればOKです。注意ポイントは、改善した工程や作業だけを見ないことです。
「1つの作業を改善したら、他の作業が悪化した」、そんなことがよくあります。全ての作業を改善の前と後で比較するようにします。
まとめ
目的をはっきりさせる
- 方針や目標を見て、ゴールを決めます
対象をはっきりさせる
- 指標を決めて、ネック工程を見つける
分析する
- 指標と工程のデータを集計して、グラフを作ります
- ネック工程、ネック作業を見える化します
改善してみる
- まずはやってみましょう^^
検証する
- 改善の前と後を全体的に見える化します
正しい改善(KAIZEN)は大きな武器になります。個人でも、会社でも改善は、大きな成長をもたらしてくれます。改善ワークをする人の参考になれば嬉しいです^^
最後まで読んで頂き、ありがとうございました。