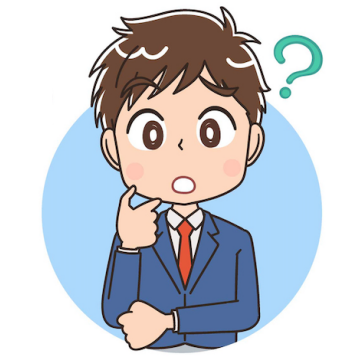
予防保全と予知保全って、何が違うの?
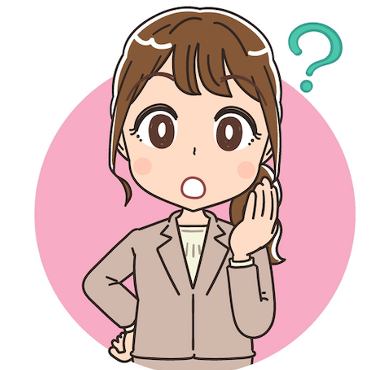
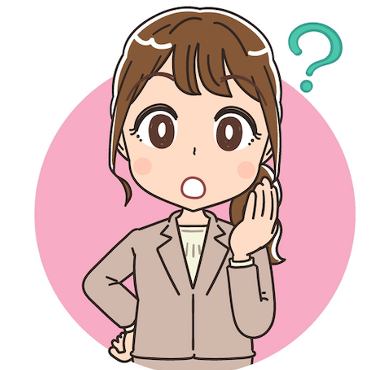
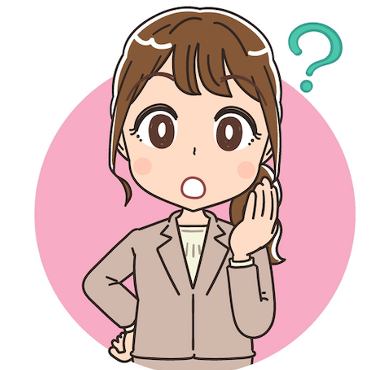
えっ、同じ意味だよね?
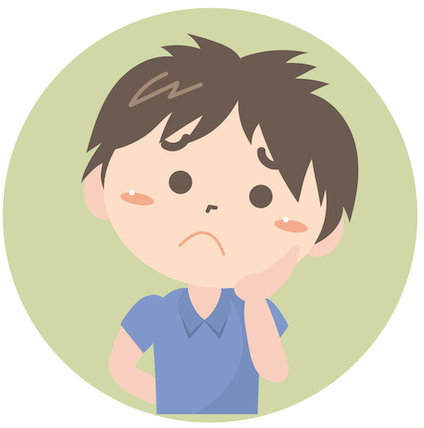
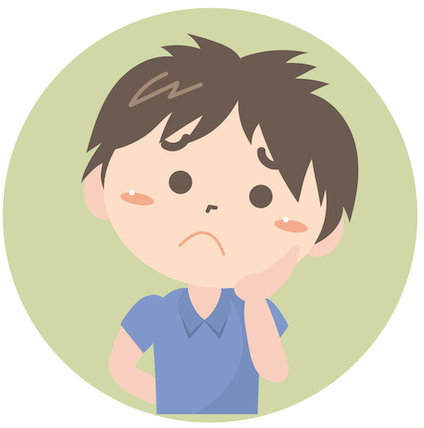
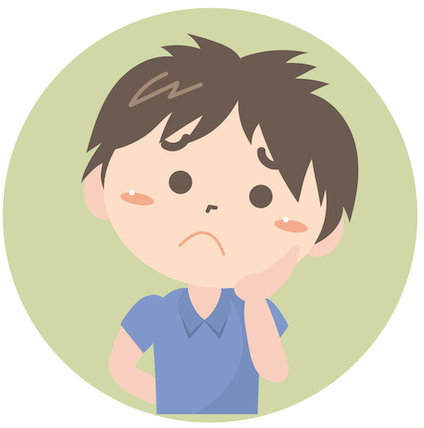
何となくわかるけど、説明できないなぁ・・
この記事は、そんな疑問を持っている人に役立つ記事です。
製造業の工場と設備(装置)は、切っても切れない縁。昔は人がメインで作業してましたが、今は機械化が進んで、なんでも装置がやってくれます。
品質の安定した製品・商品を作るためには、装置が安定して動くことが必要不可欠。
このため、IATF16949の審査では「設備管理プロセス」として、きちんと管理しているかが審査されます。
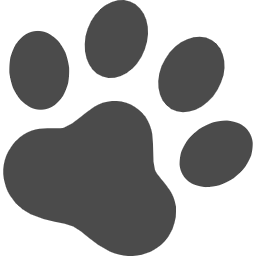
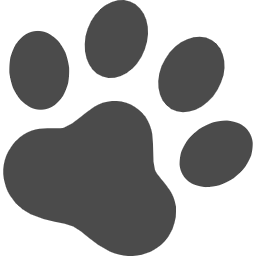
具体的な要求事項を抜粋すると
- 予防保全の活用
- 予知保全の活用
- 定期的なオーバーホール
【①~③を文書化して、運用して下さい】と書かれています。
もう少しわかりやすくすると「製品を製造する装置は、きちんとメンテナンスして使ってください」ってことになります。
TPMは、日本語にすると「総合的な生産設備管理」です。
予防保全と予知保全は、同じに見えますが、やることが違います。
- 予防保全
-
モノづくりが右肩上がりだった高度成長時代、日本企業ではトヨタ、デンソーをトップにTPM活動が盛んでした。その時、広く浸透した言葉が「予防保全」です。
予防保全は、どの会社でも一般的に使ってる言葉だと思います。
- 予知保全
-
予知保全は、まだ馴染みのない言葉かも知れませんが、予防保全を少し進化させた設備管理のことです。
2つの保全にどんな違いがあるか、具体的に説明していきます。
- 設備(装置)の管理をしている人
- IATF16949の審査で、設備管理プロセスに携わっている人
「予防保全」と「予知保全」の違いって何?
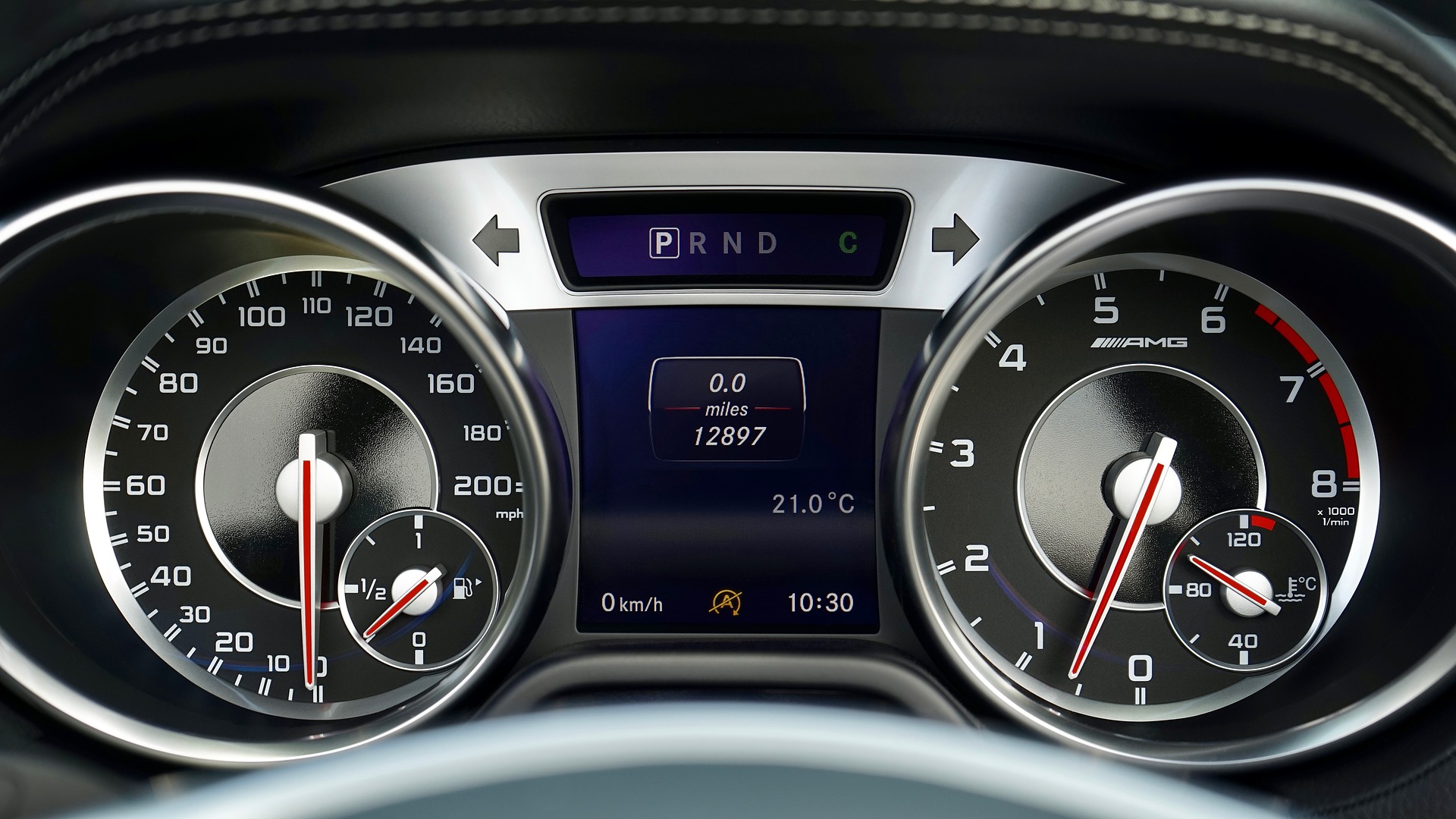
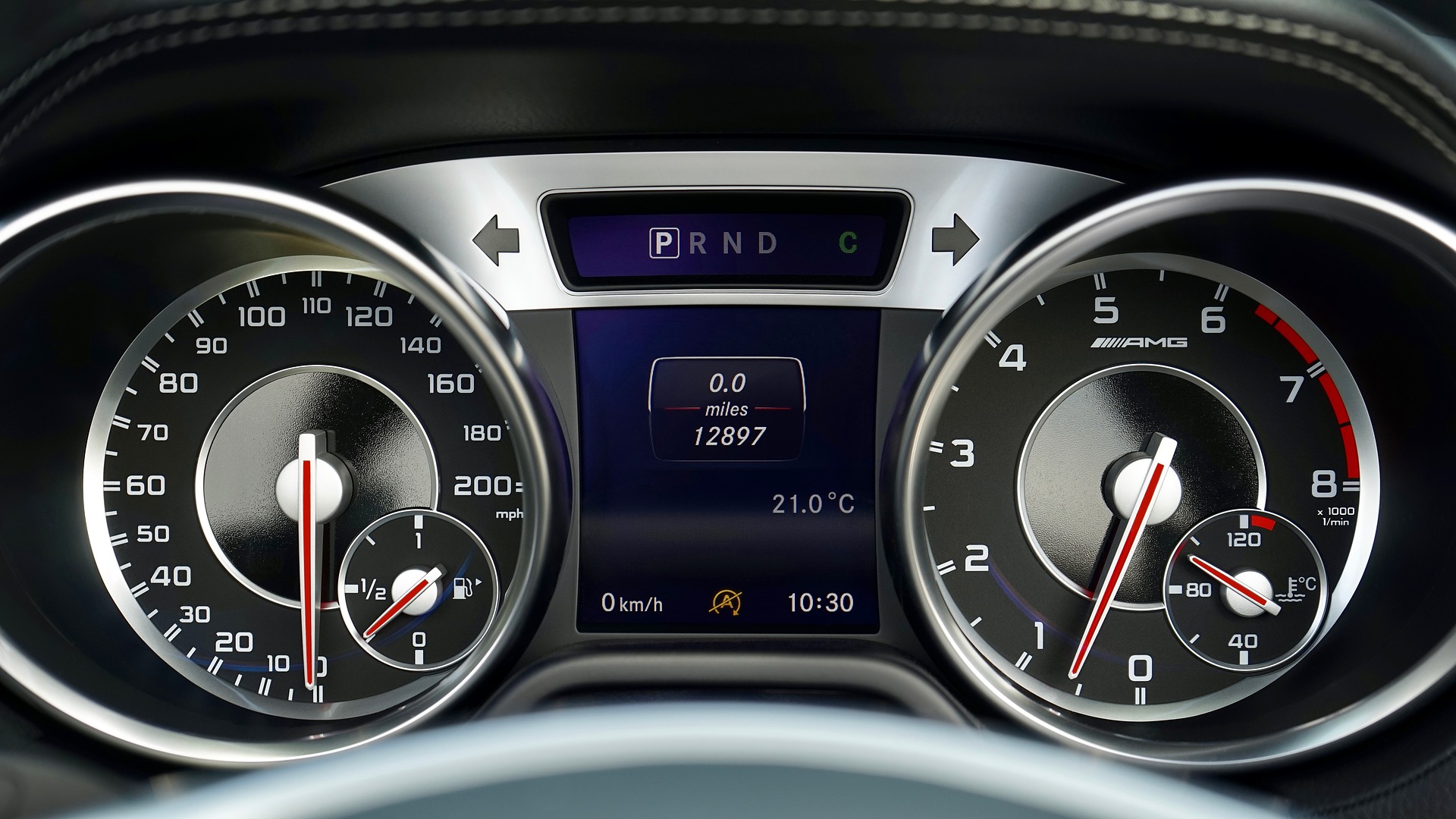
予防保全と予知保全の違いは、装置をメンテナンスするタイミングです。予防、予知の他に事後があって、3つのタイミングの違いが呼び方に表れてます。
- 事後保全:装置が故障した後に行うメンテナンス
- 予防保全:装置が故障する前に行うメンテナンス
- 予知保全:装置が故障する前に行うメンテナンス
いきなり車が故障すると、危険だし、かなり困ります。壊れる前に定期的に点検してもらって、悪い部品・劣化した部品は交換しないといけません。
部品の交換だけだと予防保全にはなりません。正しく設備が動くか検査することも含まれます。車検と同じように、検査の基準があって、検査に通るために、悪い部品を交換してるイメージです。
定期的な点検・交換よりも、定期的な機能のチェックが大切です。
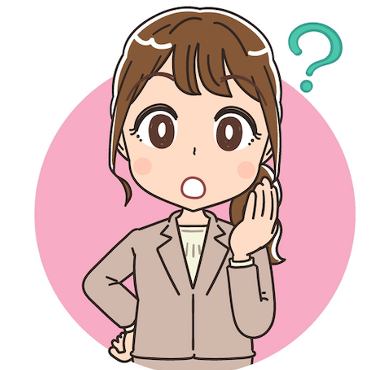
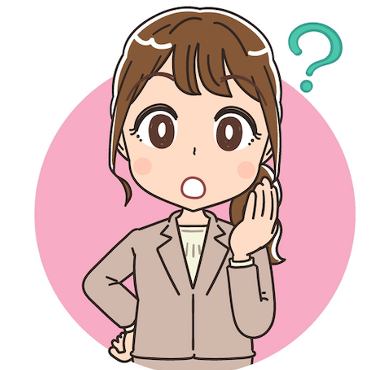
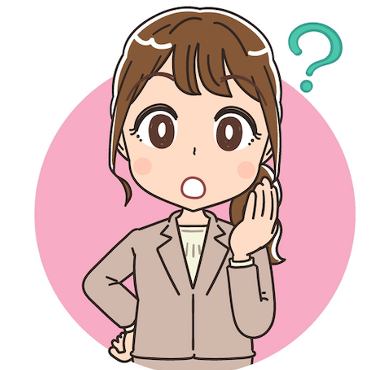
じゃあ、予知保全は?
先程の絵だと、車のパネルにある警告ランプがついてからの点検と紹介しました。警告ランプは、車の状態を常にセンサーで監視して、調子が悪くなると点灯します。
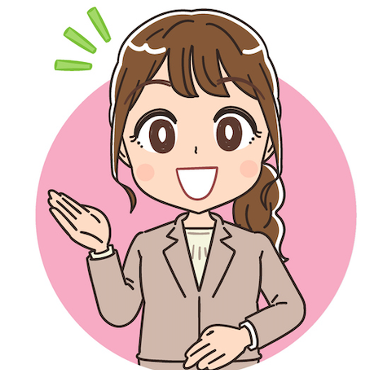
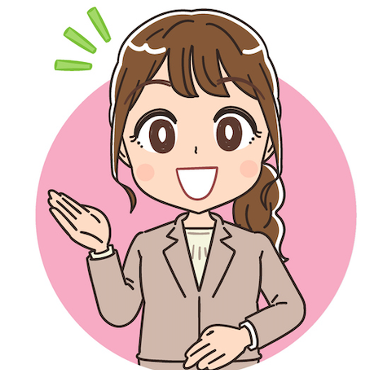
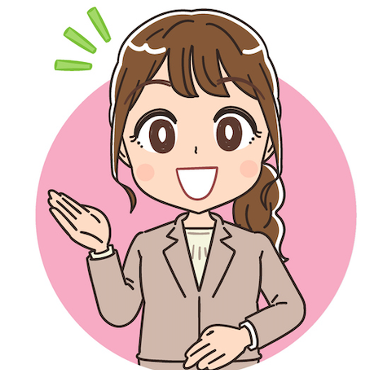
それなら予防保全(定期点検)だけで良いんじゃないの?
確かに予防保全をしていれば、故障することは少ないです。でもIATF16949では、予知保全を推奨しています。
ここで少し予防保全と予知保全のメリット、デメリットを解説します。
予防保全のメリット、デメリット
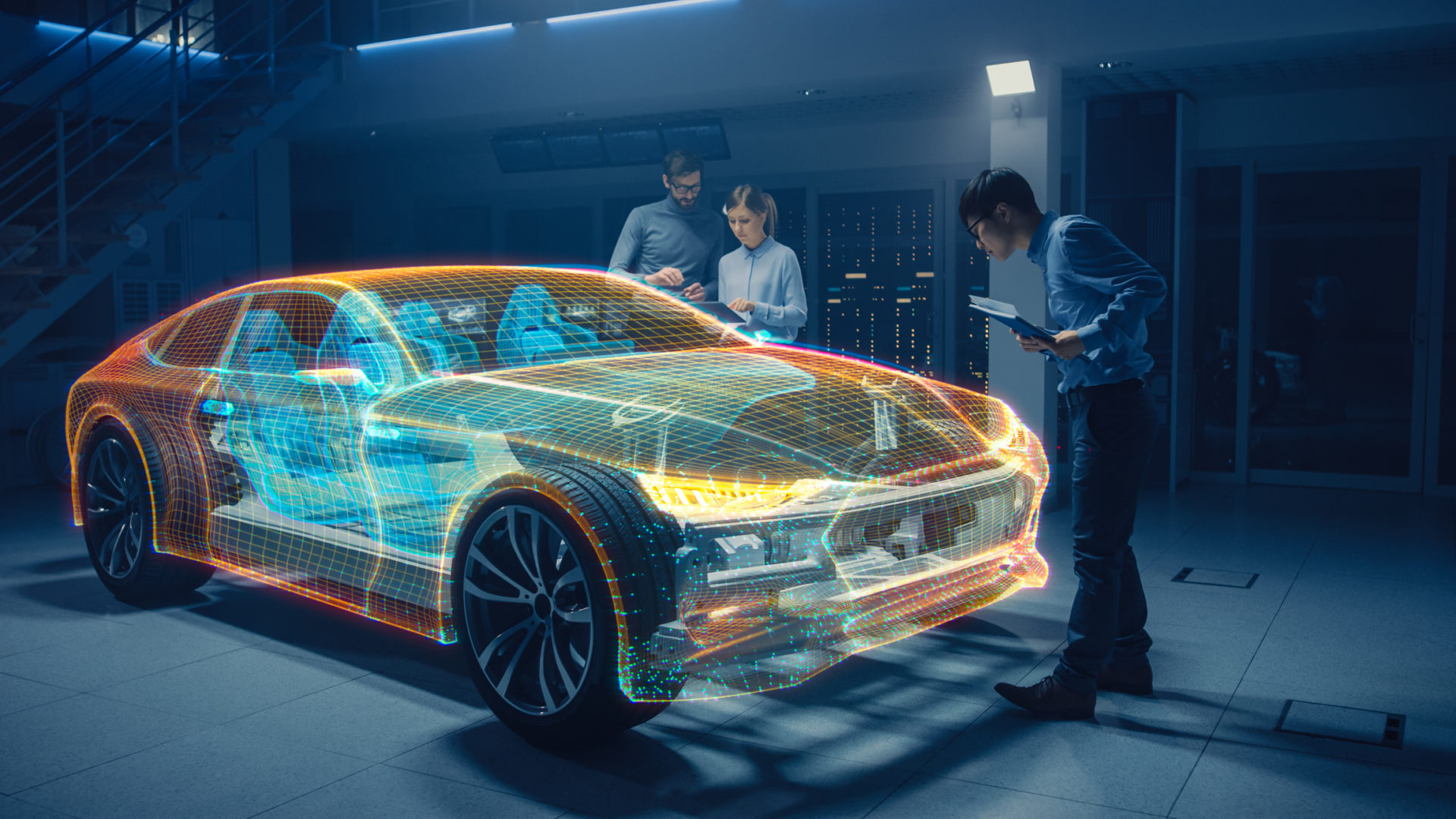
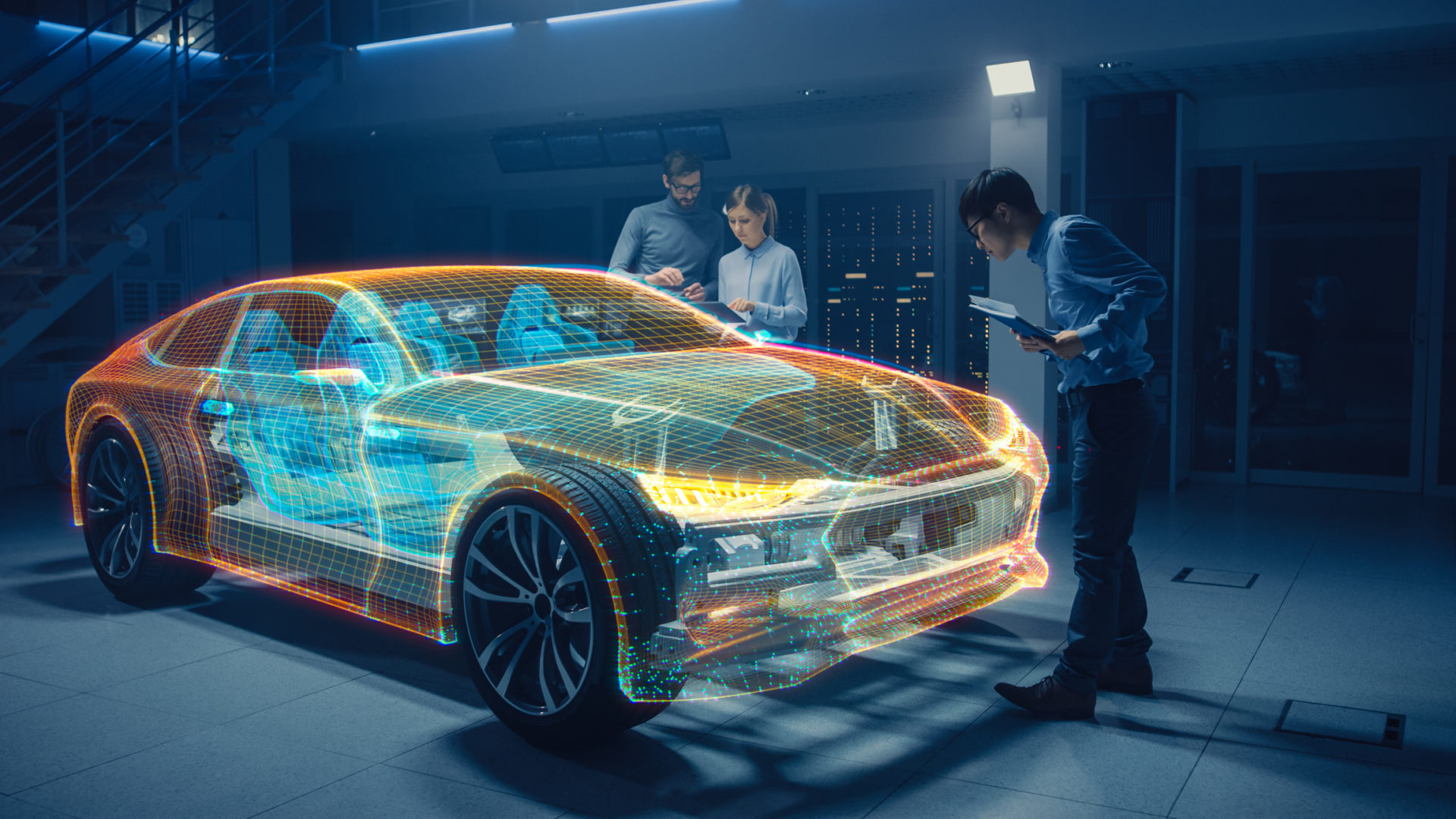
予防保全の主なメリットは、4つ!
- 点検・整備の日程を計画できる
- 点検・整備の項目を決めることができる
- 定期的に設備の状態を監視できる
- 結果、安定して設備が動き続ける
逆にデメリットは、3つです。
- まだ使える部品も交換する
- 必要なくても、期限がくれば点検する
- 必要なくても、期限がくれば点検する
予防保全は、決まった点検を、決まった期間で行うため、過剰なメンテナンスになることがあります。まだ使えるタイヤでも、車検を通すために交換した人は多いと思います。
でも、1ヶ月タイヤが使えるからといって交換しなかったら、あとで交換を忘れてしまい、大きな事故につながるかも知れません。
普通の車検は2年周期ですが、「3年でも良いんじゃない?」って思いますよね。(僕は思ってます^^;)
でも「事後が起こってからでは遅い!」って思うと、どうしても安全マージンを多めにとってしまいます。過剰管理になりがち。
このデメリットを解消しようと考えられたのが、予知保全です。
予知保全のメリット、デメリット
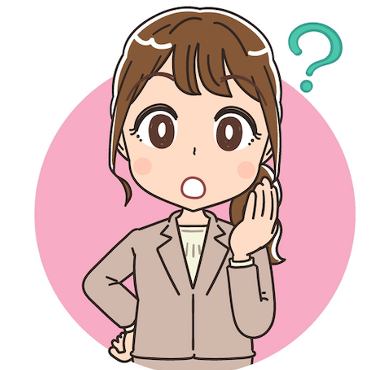
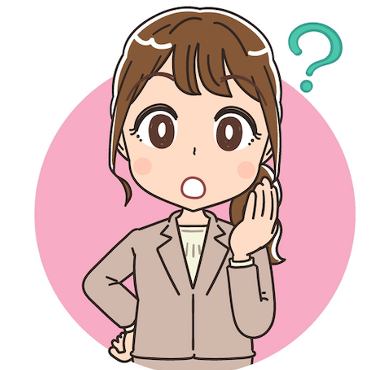
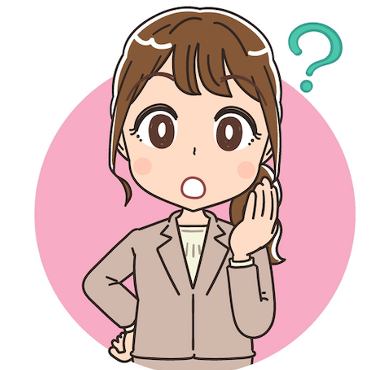
じゃあ、予知保全にはデメリットってないの?
もちろん予知保全にもメリット、デメリットがあります。
予知保全のメリットは、3つ。
- 必要なときに点検・整備ができる
- ぎりぎりまで部品を使える
- 結果、部品費用・人件費を減らすことができる
予知保全のデメリットも3つです。
- 常に装置の状態を監視しないといけない
- センサー取付けなど初期費用がかかる
- 技術的にまだ難しい
もし今の車にタイヤの減り具合やブレーキパッドの磨耗など、すべて教えてくれる警告ランプがあったら、車検はしなくて良くなります。ランプが点灯したときだけ、車屋さんに行けば良い。
実現できれば、お財布にやさしくて、飛ぶように売れるはずです。でもそんな車はありません。まだ実用段階ではないってこと。
しかし、10年前の車と比較すると、今の車は電子装備のカタマリ。近い将来、予知保全のカタマリのような車が登場するんじゃないかなぁって期待してます(^^
予防保全と予知保全の指標は?
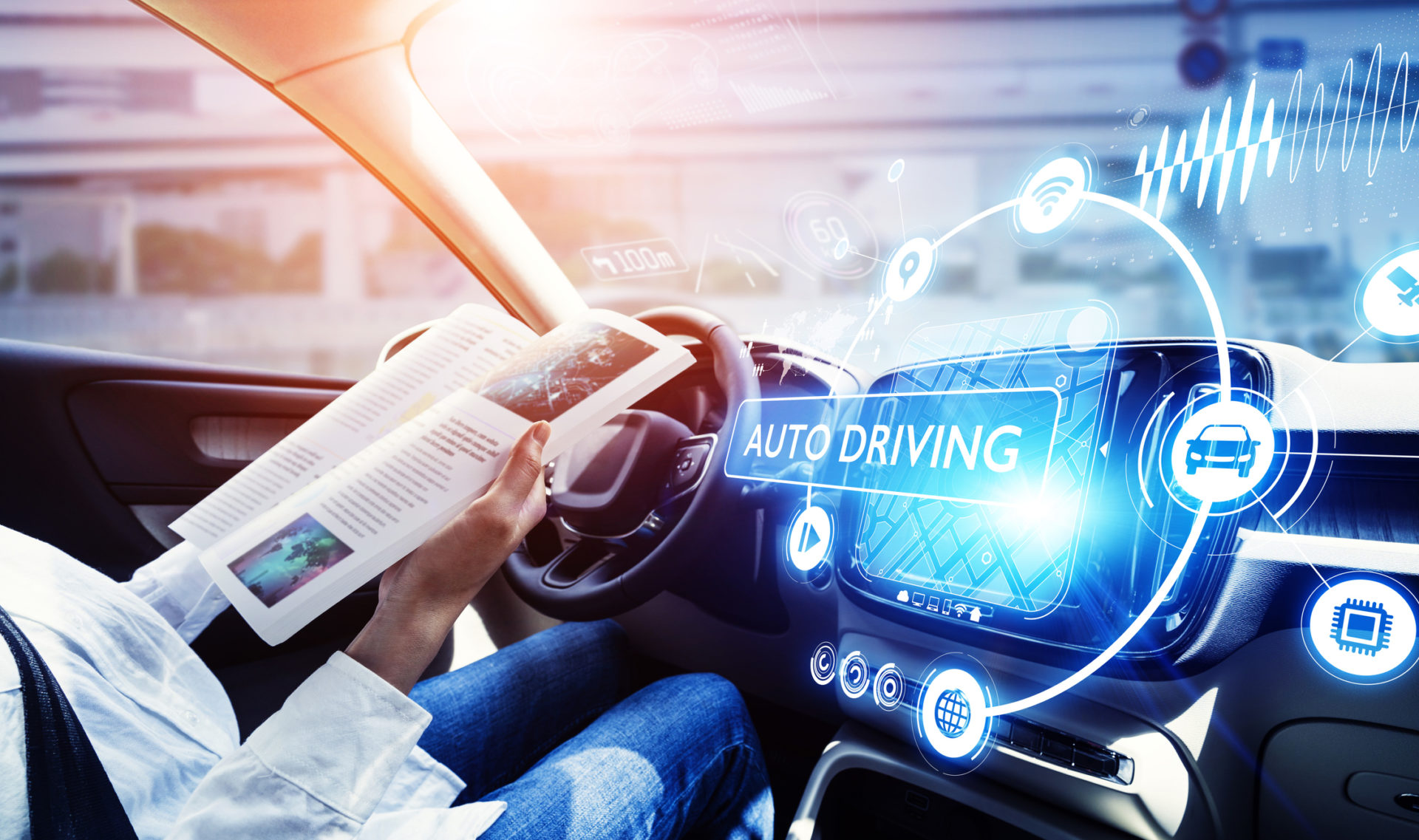
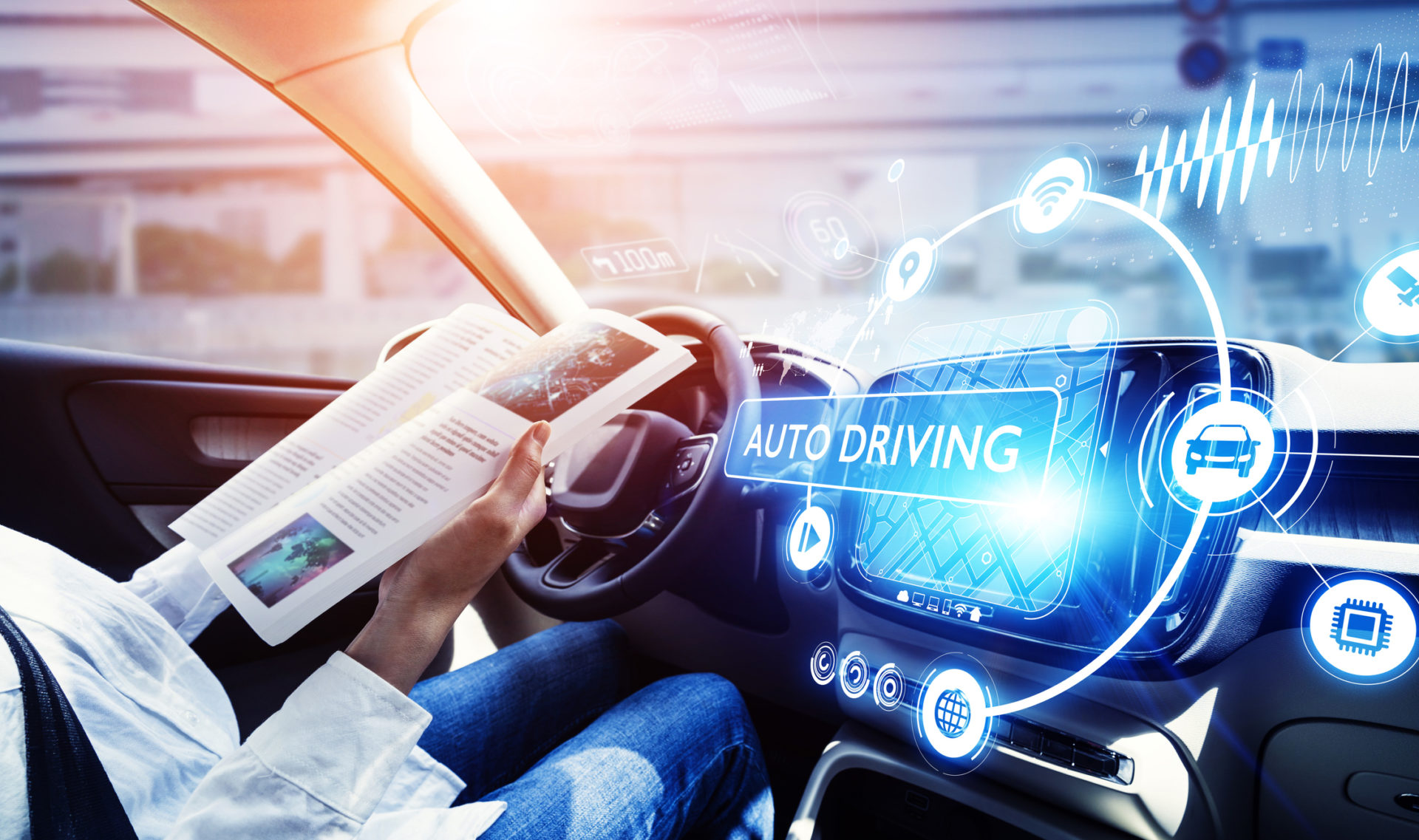
予防保全と予知保全は、どちらも装置を故障させずに、安定して動かすことを目的としています。IATF16949審査を受けると保全活動の指標をたずねられますので、その指標についても少し説明します。
指標は、保全活動がうまくいっているのか、ダメなのかを判断する材料です。
- 稼働率
- 時間稼働率(可動率)
- 平均故障間隔(MTBF)
- 平均修理時間(MTTR)
- 設備総合効率(OEE)
それぞれ何を意味するか解説します。
例として、とある工場の生産ラインを考えてみます。
稼働率
- 1日の稼働率=稼働した時間÷24時間
- 稼働率=(稼働した時間)÷(稼働日数✕24時間)
この生産ラインの1日の稼働率を計算すると
稼働率は、純粋に1日24時間の内、どの位装置が動いたかを見る指標です。このため、装置が故障した時間以外の止まっていた時間も含まれてます。休憩時間や、製品の材料がなかった場合です。
時間稼働率(可動率)
- 時間稼働率(可動率)= 稼働した時間 ÷ 計画した稼働時間
この生産ラインの1日の可動率を計算すると
時間稼働率(可動率)は、稼働率から停止した時間を除くため、より装置自体のコンディションが反映された指標です。装置の安定した動きを見るためには、稼働率よりも良いと言えます。
「かどうりつ」と言葉にすると間違いやすいため、稼働率を「かどうりつ」、可動率を「べきどうりつ」と呼ぶことがあります。
平均故障間隔(MTBF)
- 平均故障間隔(MTBF)=稼働した時間÷故障回数
この生産ラインのMTBFを計算すると
平均故障間隔(MTBF)は、故障しないでどれだけ長く設備が動いたかを見る指標です。このラインだと、平均8時間は故障せずに装置が動いてることになります。装置の安定を見る上では、設備管理の指標に向いています。
平均修理時間(MTTR)
- 平均修理時間(MTTR)=修理にかかった時間÷修理の回数
この生産ラインのMTTRを計算すると
平均修理時間(MTTR)は、故障した後に復帰するまでの時間を見てる指標です。故障している時間を減らすことができれば、生産活動に大きなプラスになります。
修理する人のスキルや、危機管理能力に関係するため、この指標も設備管理として使われることが多いです。
設備総合効率(OEE)
- 設備総合効率(OEE)=時間稼働率✕性能率✕良品率
この指標は、設備管理単独ではなく、最終的なアウトプットを見るもので、多くは顧客や経営陣から求めれることが多いです。それぞれの用語を説明します。
- 時間稼働率
-
先に説明した可動率のことです。計画した停止時間を除いた稼働率を表します。
- 性能率
-
性能率は、設備が100%の状態で生産できる理論的な製品の数量に対して、実際に生産した製品の数量です。
例えば、1日に1,000個の生産能力がある設備で、実際に作った数が900個だったら、性能率は90%になります。(900個÷1,000個✕100%)
- 良品率
-
良品率は、生産ラインに投入した数量に対して、完成した製品の数です。製品を作ってると不良品になることがあります。
例えば、1,000個作る予定で、材料を投入した結果、900個の良品ができた場合、良品率は90%になります。(900個÷1000個✕100%)不良品は100個です。
製品を作る上で大切な要素が全て含まれてるため、この数値を見れば、その生産ラインの実力がすぐに分かります。
設備総合効率は、設備管理以外の要素が多いため、設備管理の指標というより、経営管理の指標に向いてます。
まとめ:違いはメンテナンスのタイミング
予防保全、予知保全、保全の指標について説明してきました。
- 予防保全とは、定期的に設備のメンテナンス、機能の確認を言います。
- 予知保全とは、設備の状態を常に監視して、必要なときにメンテナンス、機能の確認することです。
- 保全の指標には、平均故障間隔(MTBF)、平均修理時間(MTTR)がオススメです。
- 設備総合効率は、経営指標に向いています。
本記事は以上です。
最後まで読んで頂き、ありがとうございました。m(_ _)m