製造工場でお客様の監査を受けると
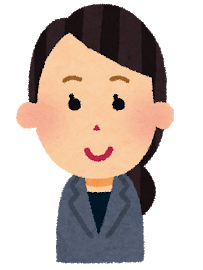
OCAPについて説明してください
って言われることがあります。
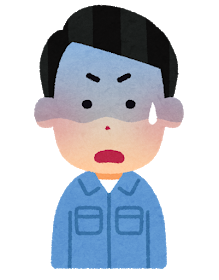
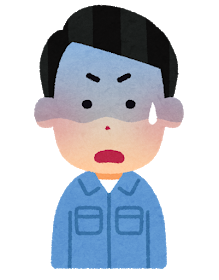
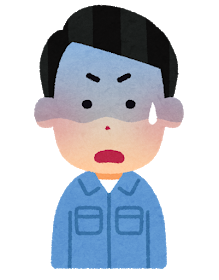
・・おーきゃっぷ???
初めてこの質問をされたとき、ちょっと頭の中が真っ白になりました^^;
体感ですが、少し前からお客様の監査で、OCAPについての質問が増えてきたような気がします。この記事では
- OCAP(オーキャップ)って、なに?
- 具体的に何をすれば、いいの?
- 監査する人に、どう答えればいいの?
そんな疑問に答えていきます。
事前に内容を把握して準備しておけば、監査なんて怖くありません^^
- 製造業の品質管理業務をしている人
- 製造現場の管理をしている人
- お客様の監査の対応をよくする人
動画での説明はこちら!
OCAPって、なに?
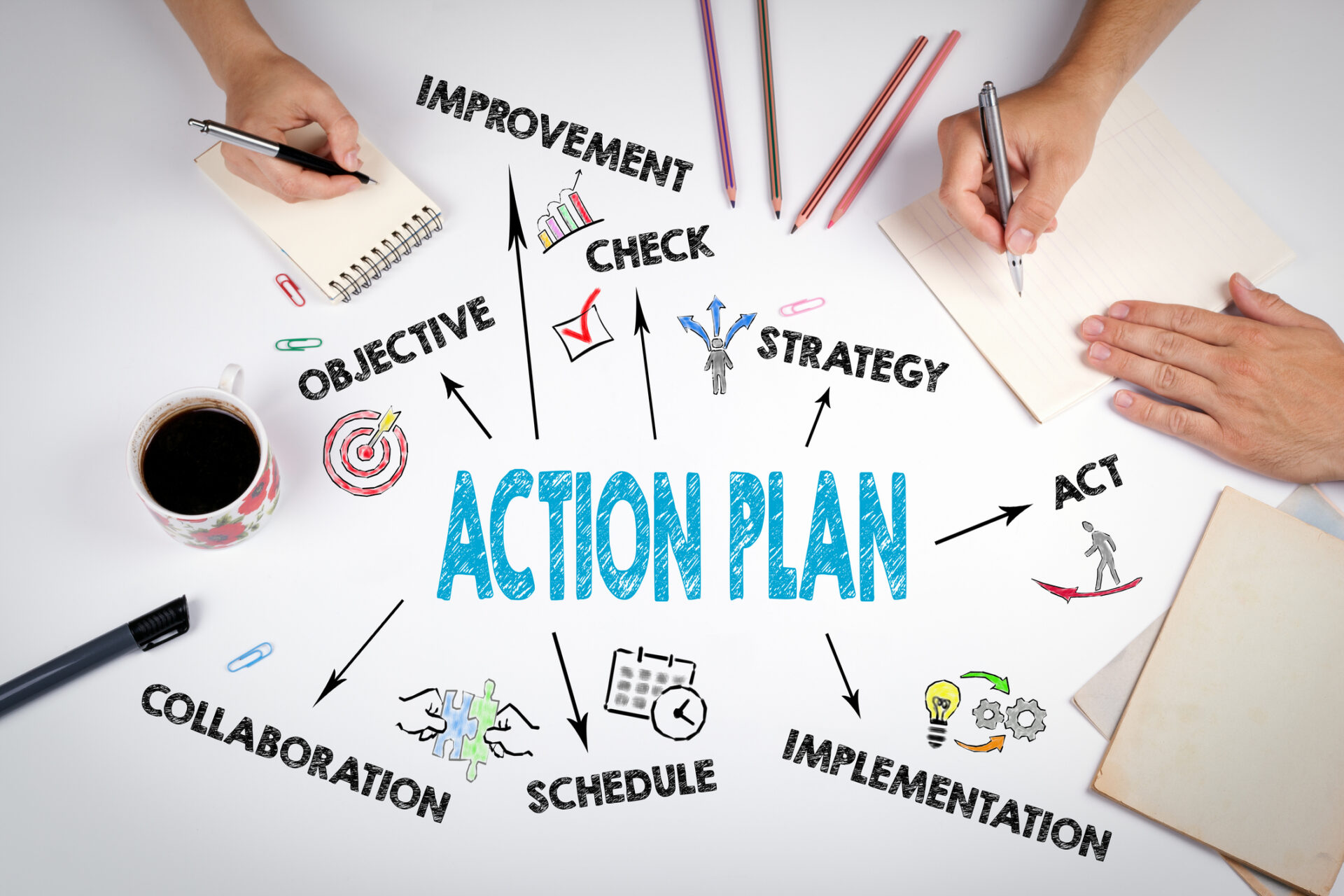
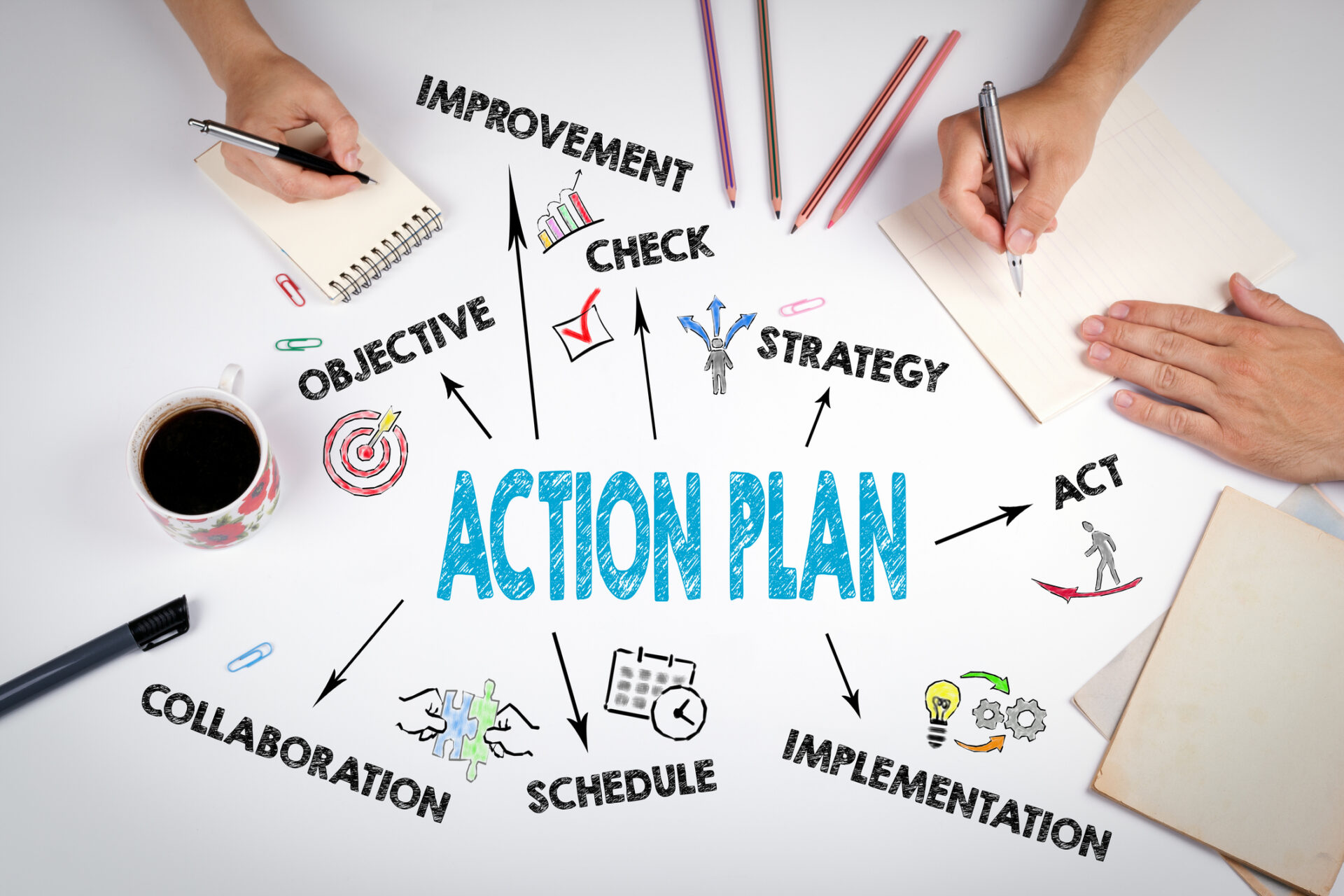
OCAPは、Out of Control Action Planの略称。オーキャップと読みます。
現場で不具合、異常が起きたときの具体的な行動を指します。
よくあるパターンは、標準書に「異常が起きたら上司に連絡する」って書かれてることがあります。でも、これだと連絡はできるけど、次に何をするのかわかりません。
上司からの指示をもらって行動するのではなく、あらかじめ次の行動も事前に決めておきましょう!って考えです。
例えば、地震が起きたら机の下に隠れましょう!ってよく言われます。
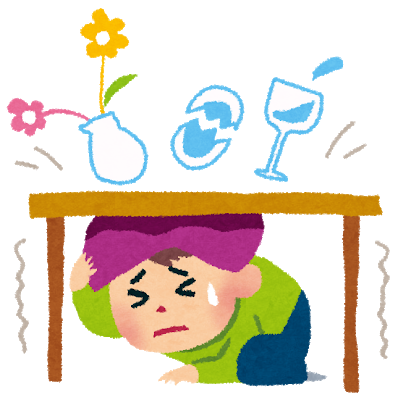
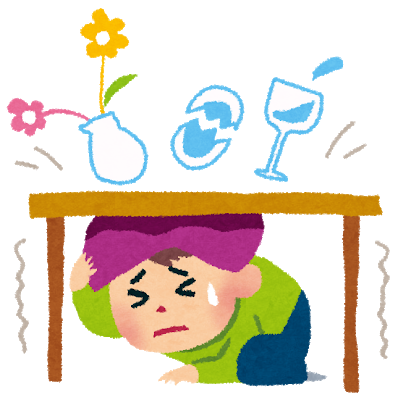
でも、隠れた後はどうすればいいのか。。。
- 余震に備えて、少し待つ?
- 台所の火を消す?
- 高いところに避難する?
いきなり地震にあうと、パニックになって、なかなか動けません。
そのために防災マニュアルを作って、あらかじめ行動すること、行動の順番を決めます。そして、実際に地震の訓練(避難訓練)をして備えます。
異常が起きた場合も同じで、防災マニュアルにあたるものがOCAPです。現場で異常が起きたときの具体的な動きをステップごとに書いていきます。
OCAPの作り方
OCAPはフローチャートを使うと、わかりやすく作ることができます。
仮に、ポテトチップの重さを量る作業をイメージしてみます。
ポテトチップの重さは60g。重さを測定して、60g〜64gなら合格、それ以外だとNGです。
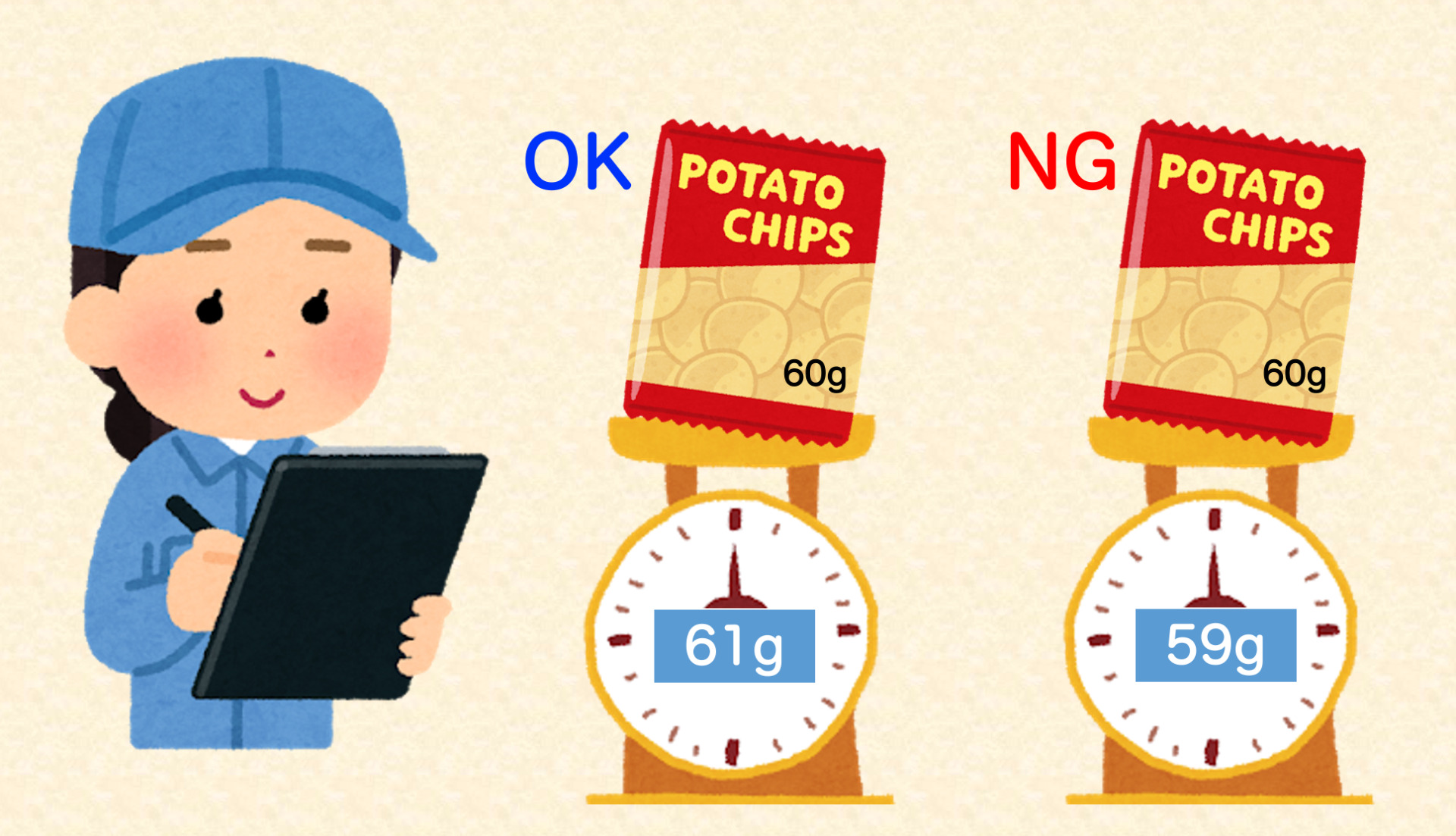
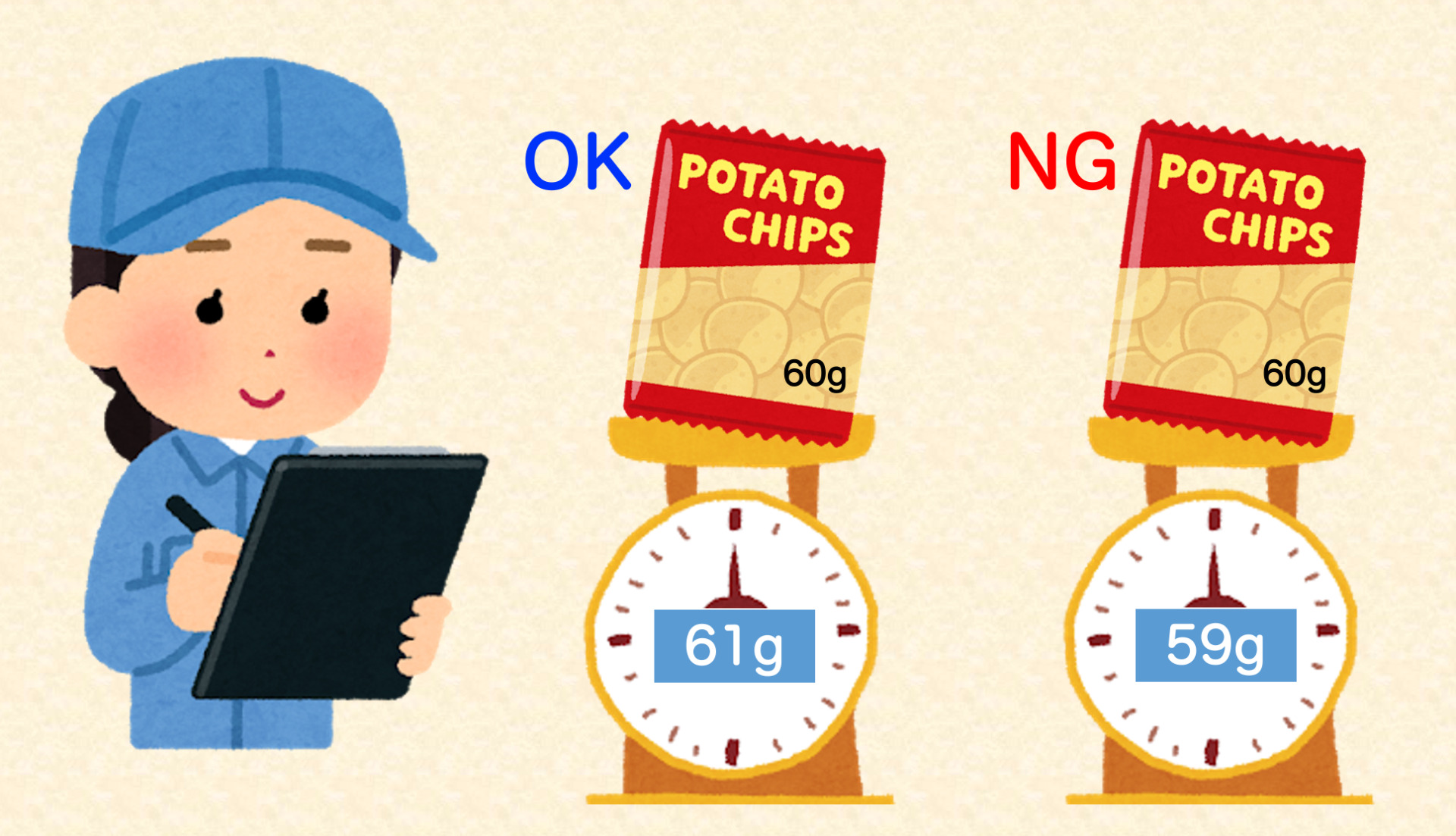
NGになった場合、どうすればいいのかをフローチャートにします。
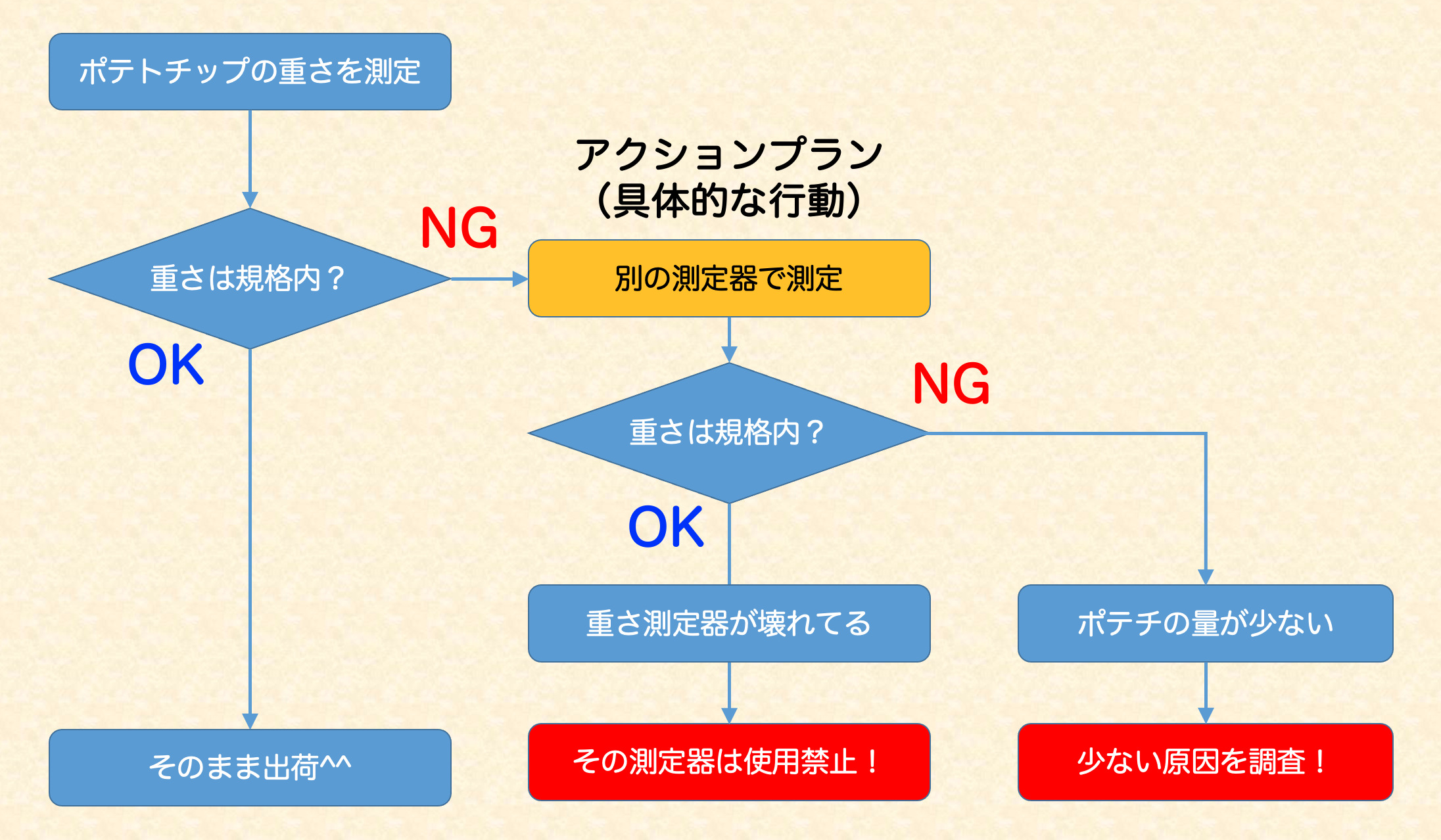
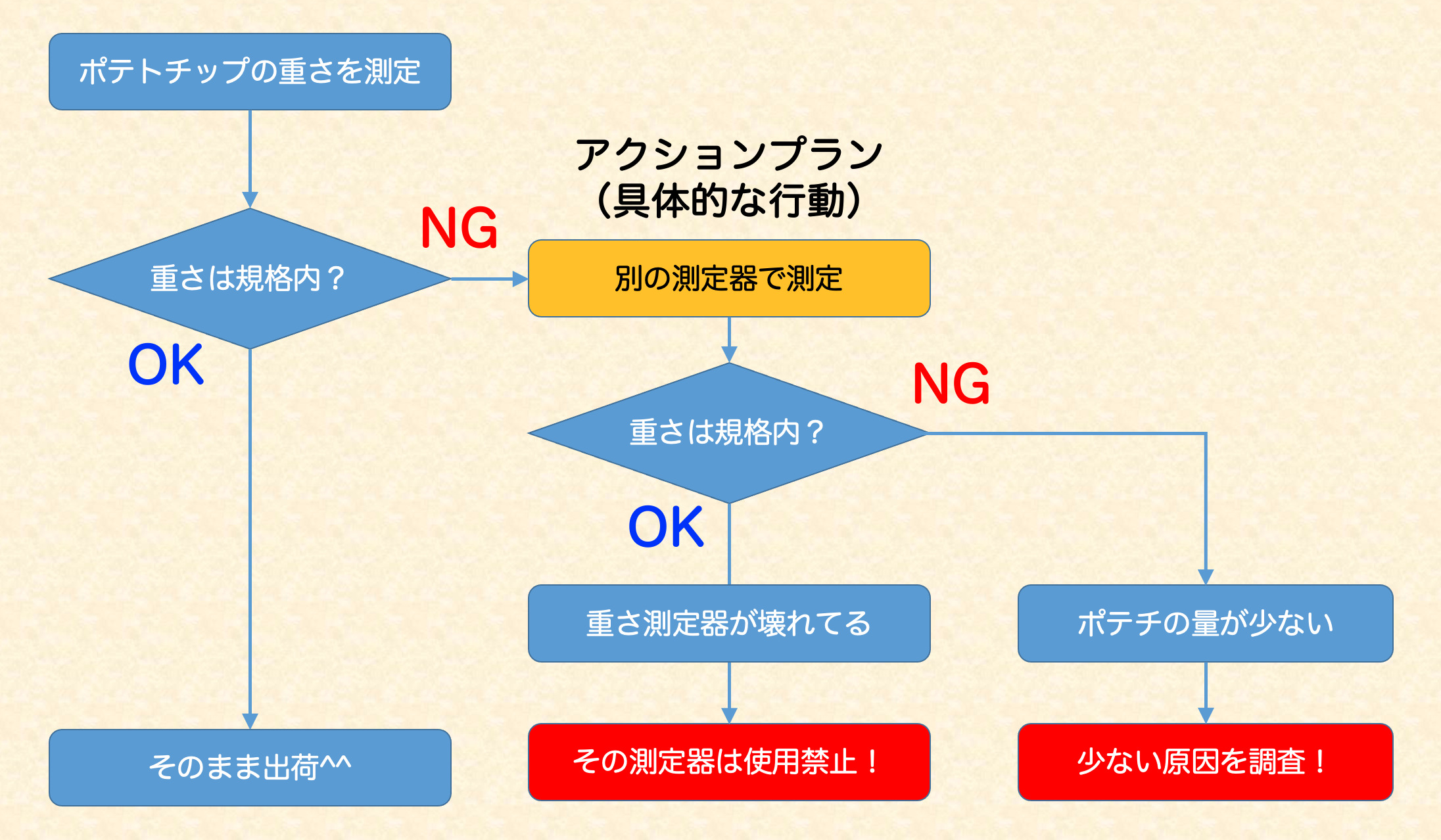
最初はNGになった原因がわかりません。原因をはっきりさせる必要があります。
- 重さの測定器が悪いのか?
- ポテトチップの量が少ないのか?
重さを別の測定器で測定します。その結果、
- 測定器が壊れてるなら、修理できるまで使わない
- ポテチの量が少ないなら、少ない原因を調査する
そんな判断ができます。
ポテトチップの量が少ない原因は、機械の故障が考えれます。
悪い場所を見つけるために、調べることまで決めておくと、復旧までの流れがスムーズになります。
- ポテチの袋は破れてないか?
- ポテチのカットが小さくなってないか?
- 袋に入れる場所のセンサーは機能してる?
最初は調査項目が少ないかも知れませんが、実際に経験したことを文書で残しておくと、忘れずに次に活用できます。
OCAPのレベル分け
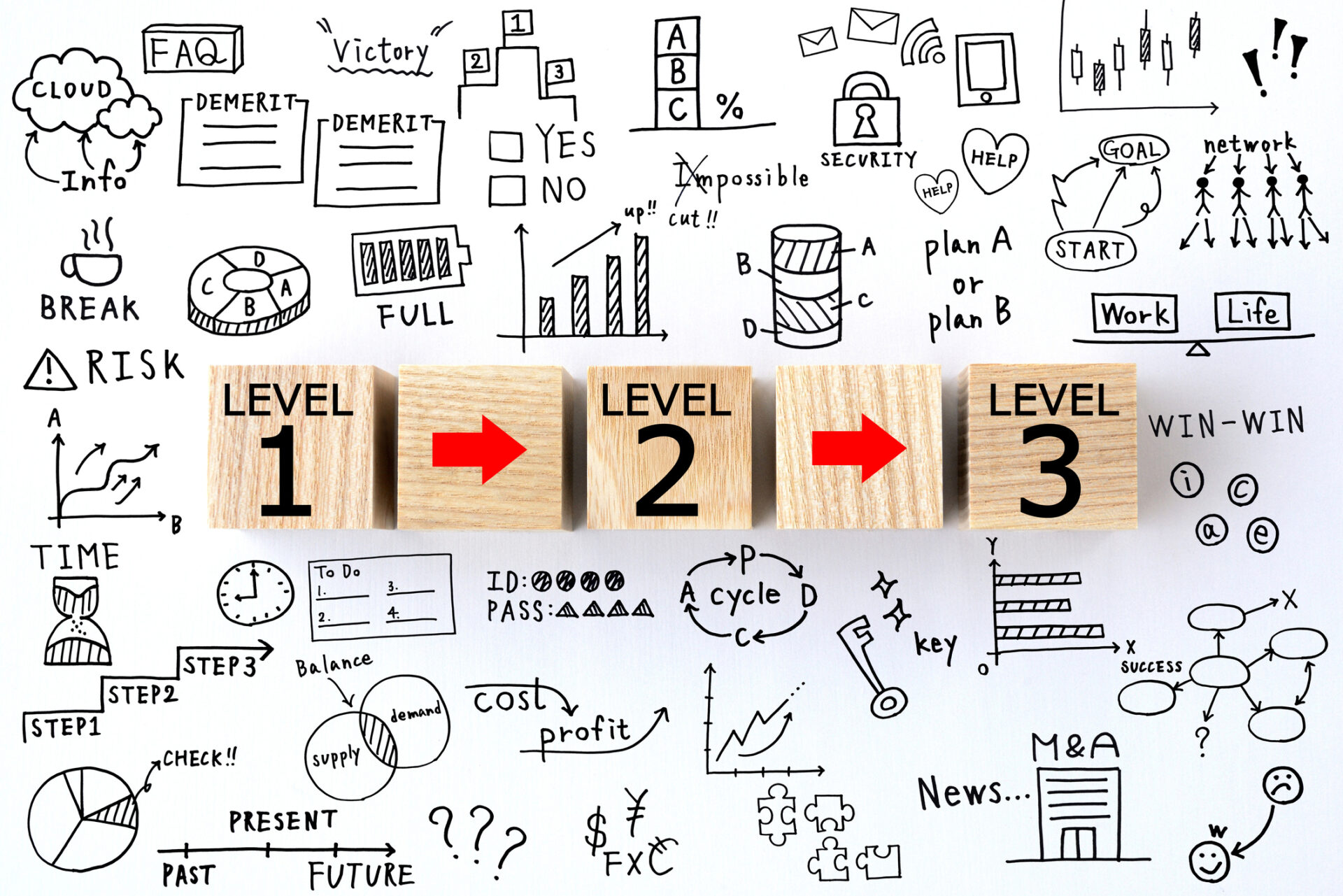
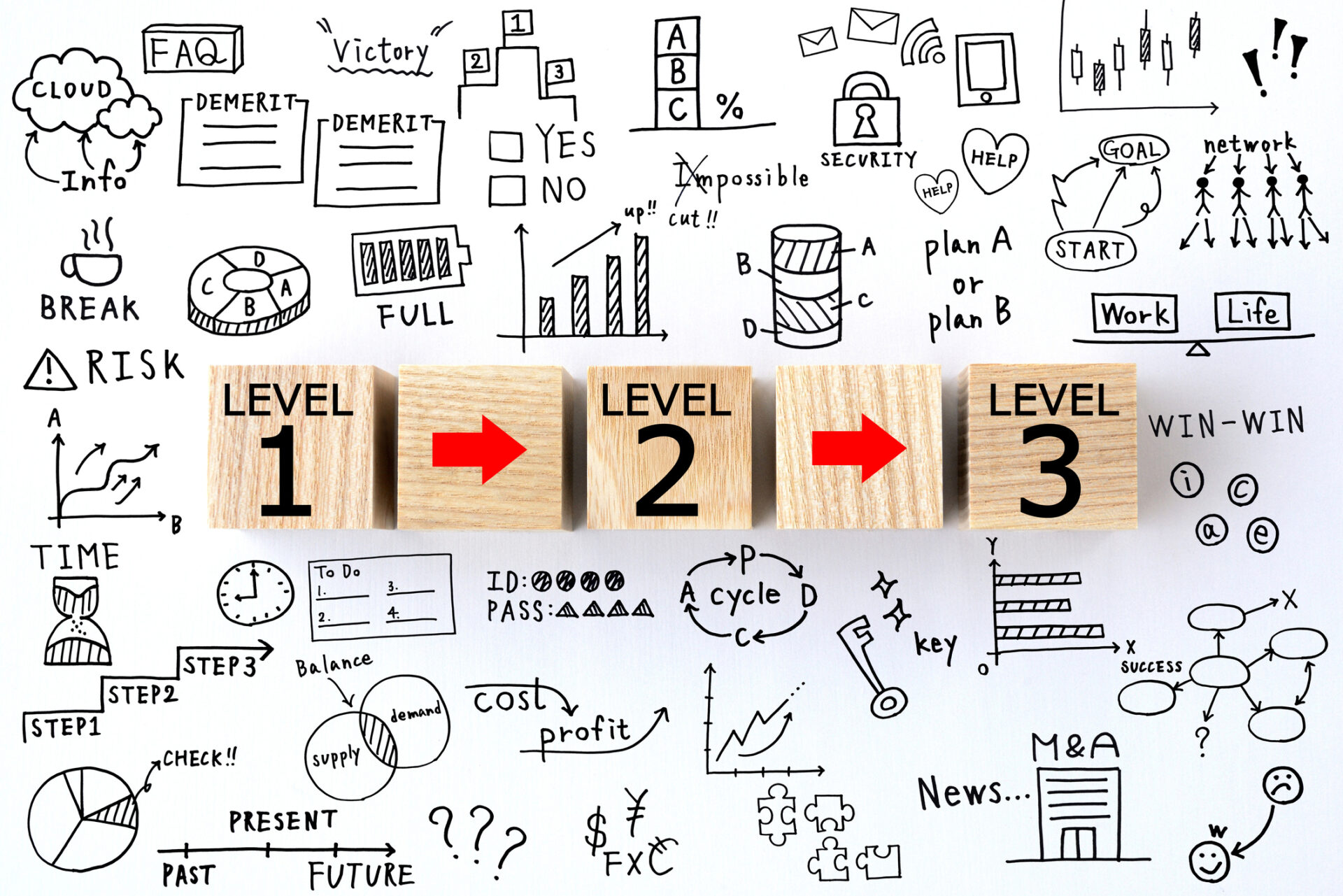
異常の内容にも、深刻な問題と、軽微なものと大きく3つレベルがあります。
ざっくりしたイメージは、こんな感じ。
異常レベル | ポテトチップ | 機械 | 原因の調査 |
---|---|---|---|
規格外れ | 不良品 | 稼働停止 | 実施 |
管理値外れ | 良品 | 稼働停止 | 実施 |
傾向管理外れ | 良品 | 稼働OK | 実施 |
- 規格外れ
-
製品が不良になる規格外れが、1番重大な異常です。
- 管理値外れ
-
管理値外れは、不良になる前の段階なので、機械を一旦止めて、原因を調査すればOKです。
- 傾向管理外れ
-
傾向管理外れは、これから不良になることが予測される段階なので、機械を動かしつつ、原因を調査すればOKです
OCAPを作るときに、この3つの異常それぞれの行動を決めておくと、よりいいOCAPになります
傾向管理の方法は別の記事で詳しく解説してます。
まとめ:OCAPは異常時の行動を決めたもの
OCAP(オーキャップ)とは?
- OCAPは、現場で異常が発生したときの具体的な行動を書いたマニュアル(標準書)です。
- 何を、どの順番でするのかを、フローチャートを使って作ります。
- 3つの異常レベルそれぞれにOCAPがあると、現場の人がスムーズに行動できます。
- 3つのレベルは、規格外れ、管理値外れ、傾向管理外れ
- OCAPがあると、現場がどこまで、なにをすればいいのかがわかるため、製品、機械がムダに止まる時間を少なくする効果もあります。
- 品質、コスト、デリバリーの全てに有効ですので、OCAP作ってみませんか(ちょっとめんどいですが^^;)
それでは、またっ!